Solid timber recovery and economics of short-rotation small-diameter eucalypt forestry
This report was prepared for Future Forests Research Ltd (FFR) by Scion.
Authors:
Dean Satchell, Sustainable Forest Solutions, R.D. 1 Kerikeri, Northland 0294. +64 21 2357554
James Turner, Scion, Private Bag 3020 Rotorua 3010. +64 7 3435899
Date: June 2010
Appendix 1: Assumptions in Discounted Cash Flow Analysis
Appendix 2: Prices and values of timber in New Zealand used for estimating board prices
Appendix 3: Timber grading
Appendix 4: Sawmilling methodology
Appendix 5: Glossary of terms
Spreadsheet 1: Kaingaroa Compartment 1194 E. regnans economic value (Microsoft Excel macro-enabled workbook 3.6 MB)
Spreadsheet 2: Optimal rotation and stocking for E. regnans (Microsoft Excel macro-enabled workbook 864 KB)
Treegrower article »
Methods
Species selection
Eucalyptus regnans (mountain ash) was chosen for this study because:
- Eucalyptus regnans, being from the monocalyptus sub-genus of eucalypts, has proven to be resistant to defoliating insects in New Zealand. A number of Australian pest incursions over the last 100 years have limited growth rates of some other eucalypts, especially those in the blue gum group.
- E. regnans is a cold-climate eucalypt suitable for a wide range of sites around New Zealand, has excellent form along with fast growth and good pulpwood properties (Kibblewhite et al. 2000).
- Eucalyptus regnans has a pale straw coloured timber (mountain ash) which has distinct growth rings and an attractive ribbon appearance. This versatile timber can be steam bent and even fumed with ammonia to give the timber a rich walnut colour. The timber is light and strong and suitable for a wide range of specialty uses. Its main drawback in young material is potentially low density and thus softness (Frederick et al. 1982, Miller et al. 2000).
- Eucalyptus regnans sapwood colour is indistinct from the heartwood and does not impact negatively on the timber's appearance.
- The sapwood of E. regnans is resistant to attack by the lyctus borer. Lyctus spp., the powder post beetle, is found worldwide and attacks the sapwood of many hardwoods (Bain 1978). Eucalyptus nitens and E. fastigata, the two most commonly grown cold-climate eucalypts in New Zealand for pulpwood production, have lyctid-susceptible sapwood. The Australian grading standards (AS 2796.2 – 2006) specify that graded timber must not include lyctid-susceptible sapwood unless suitably treated. This is an additional step and cost of production which is not necessary for E. regnans, and which may meet future market resistance if pesticide chemicals are used.
Logs and harvesting
A cross-section of logs covering a diameter range of 25 - 43 cm were harvested from a stand of 18-year-old E. regnans in the central North Island (near Murupara). These had been planted at 1100 stems per hectare, and had received no thinning or pruning. This resulted in tall trees with typically small diameters (Figure 1) and few large branches. Branch-shedding was evident most of the way up the stems.
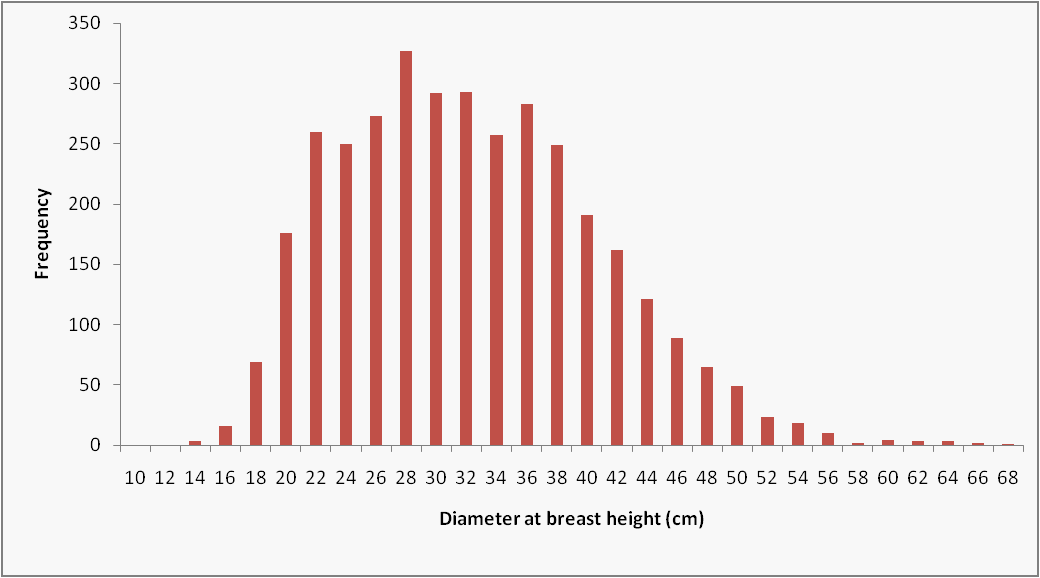
The stand was a second-generation E. regnans breeding trial and therefore represented a more diverse array of genetics than would normally be expected if planted operationally. This 1991 progeny trial comprises the New Zealand breeding population of 314 families - 160 from natural stands in Australia, 99 second generation selections, mostly from the 1979 progeny trial at Wiltsdown and 55 from APM forests. The families were planted as a single-tree-plot trial in Kaingaroa cpt 1194.
Timberlands Kaingaroa harvested 1968.3 t from 5.94 ha during April 2009, yielding 331.37 t /ha, with an estimated volume of 303.2 m3/ ha (based on individual log measurements). Individual tree volume was estimated to range from 0.5 m3 to 5 m3 (Figure 2) and log (3.3 m length) volumes ranged up to 1.4 m3 (Figure 3). Volume production is comparable with that reported by McKenzie & Hawke (1999) for a comparable treatment of E. regnans in a pruning and thinning trial at Kaingaroa Cpt 1209 and 1210. Planted at 1111 stems per ha and subsequently untended this stand had a stocking of 556 stems /ha and standing volume of 417.6 m3/ ha at age 19.
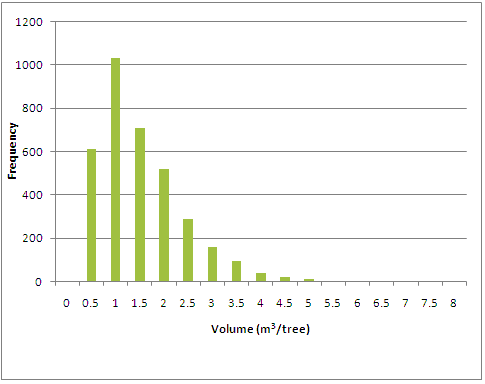
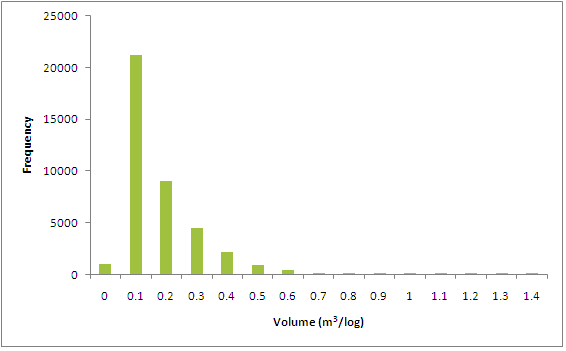
2 Estimates were made from stand data at age 16. See Appendix 1.
Logs were mechanically harvested and debarked on site on April 30th 2009. The only selection criterion was for logs to be greater than 25 cm SED. The logs provided were assumed to be a representative cross-section of logs from the stand. 28.46 tonnes of logs were transported in 6 m lengths to the sawmill on 4th May 2009. Each 6m length was cross-cut into 2 sawlog lengths one day before sawmilling; the small-end sawlogs were cut to <3 m and large-end sawlogs >3 m, giving two logs per 6 m length - these lengths were cross-cut in an attempt to optimise length to diameter for maximum sawn timber recoveries and sawmill cost-efficiency (Figure 4). This is because larger diameter logs can generally be sawn in longer lengths. When longer lengths are sawn, resulting distortion is greater over that length, requiring straightening cuts which waste more wood and produce lower recoveries. In smaller logs this wasted wood is a greater percentage of the log volume. The trade-off is that shorter log lengths, because of lower log volumes, are more expensive to mill.
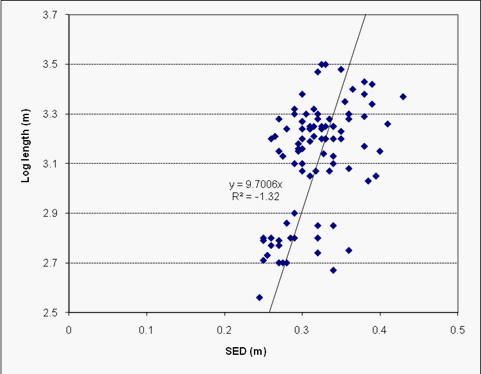
Logs were end-painted prior to sawmilling with a unique colour-code to identify the boards from each log. Total volume of the 91 logs was estimated to be 26.07 m3.
Logs had a 31.8 cm average SED, a 34.2 cm average LED and 33.0 cm average mid diameter. Logs were generally observed to have very little taper, and with an average SED: length ratio of 0.10.
Sawmilling, seasoning, machining and grading methodology
All 91 logs (average SED 31.8 cm) were milled using a Woodmizer LT 28 (with electric assist) and 3 mm kerf saw-blade.
Sawmilling commenced on 7th May and took 21 days to complete. The length of time for sawing each log was recorded. Time included initial log positioning, all sawing, slabwood bundling, fillet-stick cutting to length and bundling, along with all timber filleting into stacks. Time taken for bandsaw changes, log making and loading onto the sawmill was estimated at 5 minutes per log. Cost of sawmilling was determined using these times with an hourly rate allocated (Appendix 1).
Target sizes were predetermined and the timber was sawn into the following dimensions:
- Thickness of all nominal 25 mm boards were sawn at 28 mm;
- Nominal 50 mm × 50 mm boards were sawn at 52 mm × 54 mm;
- Sawn width of nominal 100 mm boards was 110 mm, 83 mm for nominal 75 mm boards and 162 mm for nominal 150 mm boards;
- Fillet-sticks were cut at 1 m × 28 mm × 19 mm.
All logs were halved, kept intact and turned 90 degrees, then slabbed to thickness dimension. No straightening cuts were applied when slabbing, but the two flitches are turned 180o half way through the slabbing procedure. The first slabbing cut and the first slabbing cut after turning the flitches were sawn at 54 mm. All other slabs were sawn at 28 mm. Slabs were then grouped according to width and both edges were sawn to final width dimension. Some detail on the sawmilling strategy is found in Appendix 4.
Nominal and green sawn timber recoveries (Table 2) were recorded from each log, along with milling times.
Table 2: Dimensions of sawn timber in trial.
Nominal size (mm) |
Green sawn size (mm) |
Blanked size (mm) |
Lineal m recovered |
Finished profile (mm) |
---|---|---|---|---|
100 × 25 | 110 × 28 | 96 × 23.4 | 2464.7 | 83 × 19 |
75 × 25 | 83 × 28 | 72 × 23.4 | 567.2 | 66 × 19 |
50 × 50 | 52 × 54 | 45 × 45 | 1192 | 40 × 40 |
150 × 25 | 162 × 28 | 146 × 23.4 | 360 | 128 × 19 |
Boards were filleted, stacked and weighted immediately on completion of sawmilling. Fillet spacing was 50 cm and fillets were 19 mm thick. Because boards had a slight thickness taper from the middle to the ends, care was taken to add thin timber "slivers" to fillet-sticks nearer the ends of the stack to increase the fillet-stick thickness slightly and compensate for board taper. These were inserted at regular intervals (approximately every 6th layer) to keep the stack level.
The timber was air-dried under cover for 80 days and measured using a hand-held electrical moisture meter, which then showed a moisture content of 24-30%. The stacks were then transported to a dehumidifier kiln (manufactured by J.B. Teat Ltd., Rotorua; with LAE electronic dehumidifier unit), weighted and dried for a further 23 days. The kiln reached 39oC in 24 hours and remained at this temperature for the total drying time. Humidity was set at 95% for 7 days, after which it was reduced to 75% for 4 days. Humidity was then gradually reduced to a minimum of 45% and the timber was further dried for 12 more days. Cost of contract kiln-drying the timber was $150 /m3.
Once kiln-dried, average moisture content was measured to be between 10 and 12%, meeting grade requirements.
The timber was not steam reconditioned to remove collapse, as this option was not available in the facilities used.
Boards were then dressed four-sides (blanked) at full length with a SCM superset XL moulder, to facilitate grading. Cost of contract dressing four-sides was $0.50 /lineal m.
Grading was undertaken in accordance with an interpretation of the Australian Standard AS 2796.2 – 2006, Concealed Surface grade, modified according to the specifications found in Appendix 3. The timber was graded into lengths of Select, Standard and High-Feature grades and these lengths were recorded. Short Clear Cuttings were also recorded, also defined in Appendix 3.
Cost, price and return assumptions used for estimating log value and optimal rotation length and stocking
For this study, the timber was kiln-dried and dressed four-sides to enable accurate grading of timber. The economic analysis estimated the conversion returns from product recovery volumes, product recovery costs and estimated product prices. For establishing the value of logs in terms of conversion returns we used the pricing point of air-dried timber delivered to the wholesaler. This pricing point was chosen because timber is normally only kiln-dried immediately prior to use and air-dried timber can be block-stacked and stored without deterioration while available for sale. As such, the economic analysis did not include costs of conversion from air-dried sawn timber to kiln-dried and profiled product. We are not implying that the timber is sold air-dried. Kin-dried timber value would include the additional cost of kiln-drying and finished, profiled timber the additional cost of machining, docking and grading. These costs are estimated in Appendix 1.
The economic assumptions used to estimate the conversion return of sawlogs are also given in Appendix 1. These were used in both the discounted cash flow analysis of the economic value of the study stand; and for estimating the hypothetical optimal rotation and stocking.
Utilisation and product value trials
Estimating product values for the eucalypt timber sawn in this trial can be highly subjective. Two simple trials were undertaken using the timber from this study to provide some impression of real-world value of the products sawn.
(i) Flooring and panelling
617 lineal metres of 100 × 25 mm timber was dressed into timber suitable for tongue and groove flooring (T&G) and panelling (TG&V) profiles. 62 lineal metres of defect timber was docked prior to machining. Minimum lengths were 60 cm for TG&V and 45 cm for T&G reflecting stud and joist spacing respectively. The timber was profiled at 88 × 19 mm.
(ii) Laminated panels
Six laminated panels were produced from 50 × 50 mm timber (Concealed Surface grade; one surface Select or better). These panels had a total finished surface area of 5.5 m2 , were 630 mm wide and 40 mm thick. Total cost for laminating was $250. Timber cost was based on nominal 50 × 50 mm board prices from Table A2.1, Appendix 1 and finished 40 × 40 mm piece size. Laminating included dressing, placement, assembling and thicknessing of panel blank.
Cost per square metre:
Timber cost (air-dry) | $57.50 |
Kiln-drying (at $150/m3) | $9.37 |
Blanking (dressed four sides) | $12.50 |
Laminating | $45.45 |
Total cost | $124.82 |
Next: Results »
Disclaimer: This report has been prepared by New Zealand Forest Research Institute Limited (Scion) for Future Forests Research Limited (FFR) subject to the terms and conditions of a Services Agreement dated 1 October 2008.The opinions and information provided in this report have been provided in good faith and on the basis that every endeavor has been made to be accurate and not misleading and to exercise reasonable care, skill and judgement in providing such opinions and information. Under the terms of the Services Agreement, Scion's liability to FFR in relation to the services provided to produce this report is limited to the value of those services. Neither Scion nor any of its employees, contractors, agents or other persons acting on its behalf or under its control accept any responsibility to any person or organisation in respect of any information or opinion provided in this report in excess of that amount.