Drying (Seasoning) Timber
Introduction
Drying wood is very much an art form, requiring skill, care and understanding to avoid the negative consequences of drying wood too fast or slow.
Kiln drying is usually preceded by air drying to bring the moisture content of the wood down below 30%. This allows for a more gentle kiln schedule to fully dry the timber.
Kiln drying is almost always essential for wood intended for interior uses. This is because it needs to be dried to a lower moisture content than wood will air dry to outdoors.
Most wood strength properties are improved when wood is dried below the fibre saturation pointFibre saturation point: The moisture content at which moisture is saturated within the cell walls of wood and the cell cavities are free of water. Fibre-saturation point occurs at 25% MC to 32% MC depending on the species. Below FSP water is held in wood as bound water within the cell cavities or lumen..
Some softwoods can be kiln dried from green, while most hardwoods and some softwoods should be air dried to fibre saturation point before kiln drying to equilibrium moisture contentEquilibrium moisture content (EMC): The moisture content at which wood neither gains nor loses moisture when surrounded by air at a given relative humidity and temperature. of the environment into which the wood is going.
Lower density wood generally dries faster than wood with higher density.
Thicker boards should be dried slower.
Air Drying
Air drying is a low cost and low energy method of drying timber. However conditions must allow the timber to dry slowly and evenly to avoid degrade. If dried to fast checking, collapse and deformation will result. The initial stages of drying are the most important to avoid degrade.
Freshly sawn timber should not be left block-stacked, especially if the weather is warm. Fungal discolouration of the timber can occur very quickly, especially if sapwood is present. Only durable heartwood can be block stacked for any period of time.
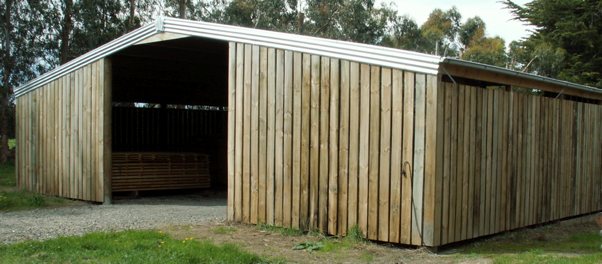
Greensawn timber should be protected from sun and wind prior to filleting.
The base
Stacking and air-drying of timber requires care and attention to detail for good results. For removeable foundations a perfectly level base of bearers is prepared. There must be sufficient space between the ground and the top surface of the bearers to allow for plenty of air movement under the stack (15 cm may be adequate, 30 cm is ideal). Weeds should be removed. There should be good surface drainage and minimal ground moisture. The two end bearers can each be levelled and a string-line attached between them, from which the rest of the bearers between them are levelled. The ground must be firm/compacted so that it does not sink under the weight of the stack. Spacing between bearers should reflect the type of timber being stacked, but is usually 1 m. For hardwoods the spacing between fillets should be no more than 50cm, with bearers under every second line of fillets, while for softwoods spacing between fillets can be up to 1m between fillets (i.e. with a bearer under every line of fillets). When the timber is stacked the fillets must be lined up vertically
Note bearer every second line of fillets for hardwood above each other from the bearer below. Before stacking timber a fillet is placed on every bearer.
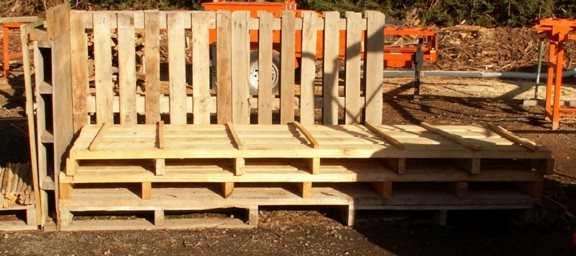
Bases may be positioned on top of the bearers before stacking timber. These bases may be constructed much like "extended" pallets, to allow easy forklift handling of stack sections. This way a forklift can keep adding stack sections to the stack, and to a height that can be safely handled by the forklift. If a stack isn't separated into sections it will not be possible to handle the weight of the whole stack with a forklift.
Prevailing wind may need to be taken into consideration when building the stack. If shelter cannot be provided the end of the stack (rather than the side) should face the prevailing wind.
Building the stack
Fillets must align vertically, directly over each other
These fillets are not directly over each other! to hold the weight of the stack above them. Timber of a consistent length is easier to stack. Where timber shorts produce a space above a fillet, short sections of fillets of the same thickness as the timber being stacked can be used to fill the gap, thus keeping the stack level.
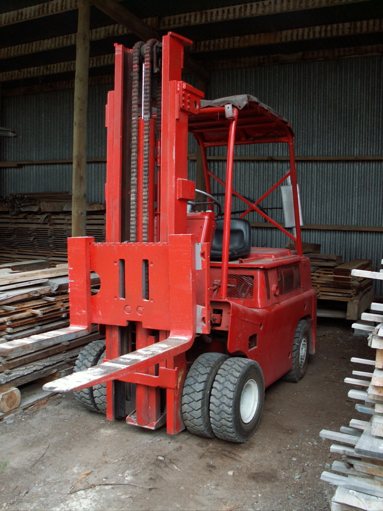
Attention needs to be paid to keeping the width of the stack consistent and without any lean. Outer boards should be placed first and lined up carefully.
Freshly sawn "green" fillets should only be used if the stack is immediately covered, otherwise there is a risk of fillet-staining.
Fillet size contributes to the speed the timber will dry. Thicker fillets mean more air movement and faster drying. Hardwood is usually dried with 10-19 mm thick fillets, with 20-25 mm thick fillets used for softwood.
To aid handling the stack with a forklift, the stack can be divided up into sections. Each section is divided by pre-made bases or alternatively 100 x 50 fillets ("gluts") to allow forks easy entry. Each section should not be heavier than the forklift can handle. Stacks should never lean, unstable stacks are dangerous
The cover
Timber being air dried must be covered. If the stack is not covered rain wll penetrate into the stack and cause fillet stains and discolouration of sapwood leading to decay. Often sheets of corrugated iron are used but these must not leak. Drying sheds are expensive but effective. What must be prevented is water penetrating into the centre of the stack where air-movement is minimal and the timber will stay wet. Covers will need to be restrained to prevent uplift.
Covering the stack also allows the timber to dry evenly. Timber nearer the top of the stack is more likely to dry too quickly and thus requires a higher level of protection from sun and wind. Covering the sides with hessian or shadecloth may help to slow the airflow. Building a group of stacks in close proximity also reduces airflow.
Weighting the stacks helps reduce distortion in the top layers of timber. Weighting must hold down the timber evenly over the top surface of the stack. Waste slabwood can be used or special
concrete weights
This concrete weight can be easily moved with a forklift can be made.
Seasonal weather differences should also be taken into account when drying timber. Drying can take place too fast in summer and too slow in winter. In summer heat can build up under the cover and dry the top layers of timber too fast causing warping, splitting and checking. It is advisable to weight the stack well and use a layer of buffer material such as slabwood on top of the stack and under the iron. The top two or three layers of boards should be lower quality seconds. Overhead shading is beneficial for summer drying, such as that provided under trees. Shadecloth can be used for the sides of the stack to slow airflow and drying. During winter drying of timber is slowed, but provided the stack is covered well so that rain does not penetrate and there is reasonable air-flow through the stack, the timber will not deteriorate.
Some durable timbers can be left stacked in the weather and in fact can be "conditioned" this way in order to slow the drying process. In general, however, sun and rain are not conducive to drying of timber.
Determining moisture level
Timber will continue to lose moisture until it reaches an equilibrium with the environment around it, at which point it neither gains nor loses moisture. This is called the equilibrium moisture contentEquilibrium moisture content (EMC): The moisture content at which wood neither gains nor loses moisture when surrounded by air at a given relative humidity and temperature. (EMC). The EMC will change as the relative humidity and temperature of the surrounding environment changes.
Once the moisture is below 30% the timber can be kiln-dried. If air-dried to 20% MC the timber can be block-stacked indoors without risk of decay. Measuring moisture levels can be undertaken with a resistance meter which measures conductivity between two probes shoved into the wood. For accurate readings wood must be clean, with no decay. A general rule of thumb for air-drying is "one year for every inch of thickness".
Kiln Drying
The rate at which timber is dried in a kiln must be carefully controlled by air temperature, humidity and air flow. To avoid excessive evaporation from board surfaces the air in the kiln must be kept relatively humid.
Generally speaking, difficult species should be dried slowly because higher rates of drying will develop greater stresses in the timber which may cause cracking and distortion. Moderate temperatures and adequate humidity levels allow timber to dry more slowly. Higher temperatures and higher levels of moisture extracted mean faster drying but with a higher risk of degrade.
Once below 30% MC ( fibre saturation pointFibre saturation point: The moisture content at which moisture is saturated within the cell walls of wood and the cell cavities are free of water. Fibre-saturation point occurs at 25% MC to 32% MC depending on the species. Below FSP water is held in wood as bound water within the cell cavities or lumen. ), wood shrinks as it dries. The rate at which moisture is evaporated from the surface of the wood must be controlled so that it equalises with the rate at which moisture moves outward from the inner wood. The drying rate is controlled by three factors: temperature, relative humidity and the rate of air circulation.
If the outer layer of wood (the case) dries more quickly than the inner wood (the core), issues encountered include:
- Shrinkage of outer layers is restricted by the moist inner wood. As this outer wood shrinks it begins to crack. This is called surface checking.
- Case hardening can occur. The surface of the board dries and shrinks which compresses the moist interior and does not allow the internal moisture to escape. Case-hardened boards when resawn will warp because the surface is in compression and the centre is in tension.
- In the final stages of drying when the core shrinks and the case is being pulled inwards, this core stress can be sufficient to rupture the inside of the board. This is known as internal checking.
- Individual cells become flattened, known as collapse or washboarding. This occurs above fibre saturation point. A drying temperature which is too high before reaching fibre saturation point aggrevates collapse. Surface and internal checks can be induced by differential shrinkages arising from collapse.
Kiln types
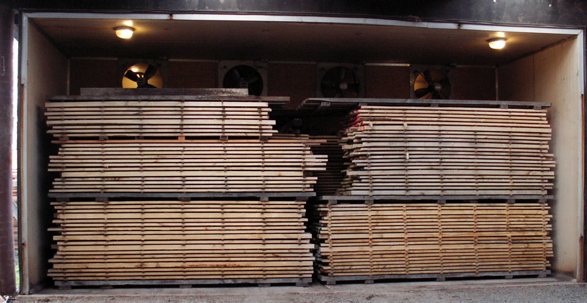
Timber drying kilns are usually conventional, dehumidifier or solar.
Conventional kilns use heat exchangers, fans and vents. The heat exchanger may utilise wood as the primary heat source to run a boiler. Cool, lower-humidity air is introduced at one end of the kiln and warm humid air is expelled at the other end. Steam reconditioning of timber can take place in the same kiln. Humidity is raised by generating steam. Humidity is reduced by discharging humid inside air and introducing dry outside air through outlet and inlet vents usually in the roof. Conventional kilns operate at reasonable costs and are used for larger installations.
Dehumidification kilns utilise an integral heat pump which supplies heat and also serves to remove humidity. This amounts to an efficient utilisation of electrical energy. However auxiliary heat may also need to be provided. As the capital cost is relatively low, this type of kiln may be attractive for small installations. Dehumidification kilns operate at low temperatures and thus drying rates are slow, producing low levels of degrade. If drying temperatures are too low freezing of the condenser coils results. Mixed species can be dried at the same time. As the timber approaches a lower moisture content their efficiency is reduced considerably because of the low operating temperatures. Because of the long drying period, good insulation is required to prevent heat losses and operating costs can be high. Furthermore, this system does not provide a means for reconditioning of timber.
Solar kilns are conventional kilns, but heat is provided via solar radiation instead of heat exchangers. Like air drying, the rate at which the timber dries is controlled by climatic conditions.
Moisture content and schedules
Kiln drying allows for a final predetermined moisture content, usually the equilibrium moisture contentEquilibrium moisture content (EMC): The moisture content at which wood neither gains nor loses moisture when surrounded by air at a given relative humidity and temperature. (EMC) for the intended end-use. This is to minimise dimensional changes in the wood product in service. The equilibrium moisture content will vary depending on use. For example the in-service average EMC is between 10-12% for interior uses in New Zealand. However this depends on climatic conditions which may vary, such as in dry centrally heated houses or permanently air-conditioned buildings.
With conventional kilns, the rate of drying is carefully controlled with a schedule. The drying is regulated to dry the wood in the fastest possible time, but without resulting degrade. Solar kilns generally take longer to dry wood because the rate of drying is not optimised. However because timber is "rested" each night, this form of drying is gentle and can produce good results.
The rate of drying is influenced by different species, the way the timber is sawn (e.g. quartersawn or flatsawn) and different thicknesses. The effectiveness of a drying schedule is measured by the level of degrade. Procedures for specifying and verifying the moisture content and quality of seasoned solid timber are set out in AS/NZS 4787:2001 Timber - Assessment of Drying Quality. Drying quality is measured by the moisture content gradient; any presence of residual drying stress (case-hardening); surface, internal and end checks; collapse; distortions; and discolouration caused by drying.
It must be kept in mind that timber does not dry at a linear rate over time. More energy is needed to remove each additional unit of water as the moisture content falls.
Steam reconditioning
Steam reconditioning can be used to offset stresses caused by moisture gradients in drying. A high temperature, high humidity treatment period at the end of drying will relieve such stress. More »).
Disclaimer: While every effort is made to ensure the accuracy of the information provided on this site, Farm Forestry Timbers Society do not accept liability for any consequences arising from reliance on the information published. If readers have any doubts about acting on any articles they should seek confirming, professional advice.