Kawa poplar timber - properties and market opportunities
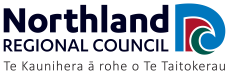
Report Date: August 2023
Author: Dean Satchell, Northland Regional Council
Acknowledgements: Many thanks to the MPI Hill Country Erosion Programme for supporting Northland Regional Council to achieve improved soil conservation outcomes and build our technical capacity.
Introduction
Poplar timber is light, soft, pale coloured and non-durable. These characteristics offer both advantages and challenges for sawn timber applications. In New Zealand poplar timber tends to be used mostly for appearance panelling, with its appealing lustre, light colour and indistinct latewood offering a unique timber product. Poplar timber has also been successfully used for truck and trailer decking and, when preservative-treated, for gates, stockyards, battens and fence posts (McIvor 2011). However, these markets are not developed in New Zealand and as a result poplar is not well known or appreciated in this country.
Appearance applications
The even, pale white colour of the wood is not likely to limit appearance markets for the timber. Indeed, this is a desirable and property, offering market opportunities as "the wood that doesn't yellow". If a darker wood is desired, poplar can always be stained, noting that poplar is highly regarded for its ability to take an even stain (Wilkinson, 2000).
A good quality clear finish brings out a very decorative lustre in the otherwise plain and flat appearance of sawn poplar timber. Because so many appearance options are available for the one timber species, it has become reasonably popular in Northland for interior decorative panelling (A. Bergman, pers. comm).
Thermal modification
Thermal modification is a technology increasingly being used in New Zealand to improve the durability of wood without chemical treatment, and to make wood darker in colour. However, bending strength of the timber is significantly reduced, thus limiting applications for the timber.
Products manufactured from thermally modified wood include cladding, decking, garden furniture, exterior door and window frames and other applications where physical strength is not important, but stability and reasonable durability performance is required. Thermally modified radiata pine is being marketed in New Zealand in the form of preservative-free appearance weatherboards that do not require paint protection. Thermally modified poplar has not been tested in New Zealand for weatherboards to date, but has been used in Europe and the USA for many years (e.g., ThermoArena, Americana). Thermally modified poplar could have market potential for cladding and window joinery in Northland, and testing here would verify durability performance and stability in service, potentially opening the door for developing markets for the wood.
Surface hardness
Despite the attractive appearance of poplar timber, low surface hardness detracts from furniture and flooring applications (Wilkinson, 2000). However, options are available that increase the density and/or surface hardness of timber for these applications.
One option is surface densification. Mechanical densification (compression under heat) improves the surface hardness of wood. Surface hardness of poplar was more than doubled by compressing the wood by 25%, from 24mm to 18mm thickness (Cai et al. 2013). However, such mechanically densified wood tends to be dimensionally unstable, i.e., it “springs back” when exposed to moisture. However, a combination of heat, steam and compression overcame this for a dimensionally stable densified product (Skyba and Schwarze 2009, Sözbir et al 2019). Combined densification and thermal treatment of poplar produced a product with potential for high value applications because of improved dimensional stability and surface hardness (Cai et al 2013). However, this process is not yet commercially available in New Zealand. Densified, thermally modified poplar could potentially yield market premiums as flooring and joinery components, depending on the required quality of the product. However, for commercialisation investors would require confidence in the technical and commercial viability of the technology, thus research and development efforts.
Surface hardness could alternatively be achieved by coating the timber with a clear polymer product that becomes harder than the timber. Clear coatings for wood benchtops and other applications have been available for some time, such as epoxy and polyester resins. However, knowledge on their application as coatings over installed timber floors, to provide surface hardness to soft woods, appears to be lacking. Polyester resins have a reputation for not sticking well to timber, while epoxy resins tend to yellow over time and scratch easily. Polyester resins can be thinned with acetone to enable the resin to "soak into" the wood and achieve improved adhesion, but would require multiple coatings before the final coating with wax included to cure the polyester. Both polyester resin and acetone are unpleasant to handle and require respiratory equipment to apply, with an unpleasant smell lingering for long periods. Epoxy resin, on the other hand, has very little smell, has become available in non-yellowing formulations and can be thinned with ethanol. Non-yellowing UV resistant polyurethane products can be applied over the epoxy to provide a scratch-resistant surface suitable for the type of wear that floors are subjected to.
Other unique properties and applications
Poplar timber does not impart taste or odour to foodstuffs (Isebrands and Richardson, 2014). Poplar could therefore potentially become subject to high demand pressure in a post-plastic packaging era for eco-packaging that is in contact with food. This market should not be dismissed lightly, noting the current "green" packaging transformation taking place due to changing consumer preferences. This property is uncommon in timbers. Kahikatea, like poplar, does not taint food and was the native species of choice for food packaging historically, being used principally for export butter boxes.
Structural applications
Poplar is reputed to be more “resilient” than pine, making it suitable for products such as farm gates (McIvor, 2011). However, "resilience" does not appear to be a measured property in timber and the available data on mechanical properties shows poplar to have both low impact bending and static bending strengths. However, although poplar is a soft timber, it is reputed to be very hard wearing, thus its utilisation and demand for wooden truck decking. This market has not been developed in New Zealand, but anecdotes abound on the virtues of poplar for this application, especially for ramps and decking for heavy machinery.
Mechanical properties and structural performance
The most widely grown clone in Northland, Kawa, has lower documented mechanical values than radiata pine, along with a lower density:
Species/clone | Modulus of rupture (MPa) at 12% m.c. | Modulus of elasticity (MPa) at 12% m.c. | Basic density (kg/m3) |
---|---|---|---|
Kawa (8 years old) | 56.9 | 5.4 | 338 |
Radiata pine (25 years old) | 85.8 | 8.2 | 415 |
This contrasts with Kawa's reputation in Northland for what is often described as "good" wood density. Wilkinson (2000) provides the basic density for 8-year-old Kawa as 365 kg/m3 and an air-dry density of 440 kg/m3. These are the only documented properties available in New Zealand for Kawa and are clearly insufficient to determine its potential for structural applications. This data shows 8-year-old Kawa poplar to have much lower working stresses than 25-year-old radiata pine, with lower properties in relation to its density. This contradicts Hunter and McIvor, (2008) and McIvor (2010), who reported that poplar has good strength properties in relation to density. Although young tree age could be a factor that provided the reported poor mechanical properties for Kawa poplar, within-cultivar density for poplar varies little between region, site and position in the tree (Wilkinson, 2000), suggesting that very little variation in strength properties can be expected from trees of all ages. This requires confirmation by testing mechanical properties from more mature Kawa trees (e.g., 25 years old). Clearly, a better understanding of strength relative to density is important for assessing market opportunities for structural Kawa timber.
Uneven density and uneven mechanical properties within and between trees are common for other wood species grown in New Zealand. Radiata pine's density and mechanical properties vary significantly within tree, between trees and between regions (Cown, 1982). A key advantage with even density and mechanical properties, if verified and documented as stress values, is that these could potentially be used by engineers and designers without the need to verify or test mechanical properties for timber from that clone. The Kawa clone could be tested for mechanical properties from different radial and vertical positions in the tree, and from trees of different ages and even from different regions, in order to assess the variability of these properties. If little variability exists within and between trees, this could unlock an important market advantage by lowering the costs of compliance for constructing buildings from visually graded poplar timber.
Although the poplar structural product might be inferior to radiata pine (Williams et al., 1986), and in most cases be in direct competition with it, the decorative qualities of poplar could generate market premiums and demand for appearance structural products such as exposed rafters, glulam beams and other products used in post and beam (portal) construction.
Limited in-grade testing of poplar has shown that working stresses were similar to medium-density radiata pine visually graded to No. 1 framing, provided adjustments were made for density; and critical joints had additional fixing (Wilkinson, 2000). Therefore, research into mechanical properties for a range of common clones would be required before utilising poplar for structural applications. Because the Kawa clone is reputed to have a relatively high wood density and good strength properties (P. Davies-Colley, pers. comm), and is common throughout Northland, testing of mechanical properties could begin with this cultivar. Further work could explore the relationship between density and stiffness across the range of commonly grown cultivars.
Preservative treatment for H1.2 applications
To be Building Code compliant, interior structural timber is required to have a minimum life of 50 years in service in the H1.2 hazard environment (protected from the weather, where there is also a risk of moisture content conducive to decay). For H1.2 applications, radiata pine, being a perishable timber, requires boron treatment to 0.4% Boric Acid Equivalent under NZS 3640 Chemical preservation of round and sawn timber. Poplar, like radiata pine, is a non-durable timber species. In order to become code compliant, evidence will be required that level of treatment is sufficient to provide durability performance equivalent to H1.2 radiata pine.
Pressure treatment of dry poplar with boron has produced unsatisfactory penetration results (T. Singh pers. comm). However, two months of boron diffusion provided boron retention well above the requirements of the H1.2 specification for both 25 mm and 50 mm thick boards (Williams et al. 1986). Boron diffusion is a simple process whereby freshly sawn timber is coated with a concentrated solution of boron (usually dipped) and then block stacked under cover for a sufficient period of time to allow the boron to diffuse into the sawn timber, before drying. The length of time for diffusion depends on the thickness of the wood being treated. A boron solution is easily prepared from 65% water, 20% borax and 15% boric acid to make a solution of 15.8% borates (BAE or boric acid equivalent).
A Similar Materials accelerated test method as per clause B2AS1 of the building code is available for comparing rate of decay between H1.2 radiata and boron treated poplar, which can determine code compliance in as little as one year (AWPC, 2015). Poplar has not undergone this test in New Zealand, so remains non-compliant with the building code, which requires proof of durability performance. This test is essential before market development can take place for H1.2 poplar for interior structural applications.
Wood modification technologies for structural applications
Chemical-free methods have been developed for increased durability and strength of wood species for specific applications. Both durability and strength have been improved for poplar wood via modification.
Heat treatment (thermal modification) is a chemical-free method for increasing the biological durability and dimensional stability of wood (Esteves & Pereira, 2009). Mass loss associated with thermal degradation increases with treatment time and with higher treatment temperatures (Esteves & Pereira, 2009). However, the high temperatures required to impart a significant increase in durability also significantly reduces the mechanical properties of the wood, in particular static bending strength (a 30-60% reduction at treatment levels required to impart significant durability) and impact bending strength (Esteves & Pereira, 2009). Impact bending is an important mechanical value for heat treated timber because a reduction to less than half the untreated timber’s value can occur (Rapp & Sailer, 2000). Impact Bending strength (otherwise known as toughness or brittleness) is important for use under dynamic loads (Bal and Bektas, 2012). For this reason, thermally modified timber does not tend to be used for structural applications.
Impact strength of unmodified hybrid poplar is nearly as high as eucalyptus and beech in relation to its density (Bal and Bektas, 2012). However, hybrid poplar thermally modified in oil at 200°C for over 2 hours decreased in impact strength by ~50% (Bak & Németh 2012).
As the temperature used for thermal modification increases, durability increases but strength decreases. Thermal modification at 230°C (e.g., Thermowood 230 process) is practiced in New Zealand for radiata pine products sufficiently durable for exterior applications such as weatherboards and bee boxes. The Thermowood 230 process achieves 225° C or greater core wood temperature for two hours (Mark Andrew, pers. comm). However, poplar thermally modified using the same process as radiata pine will not necessarily achieve the equivalent durability performance, so requires testing. Options for testing include graveyard testing, accelerated decay (cellar) testing and in-service testing for the product.
Testing poplar's strength properties and durability performance when thermally modified at 230°C is the essential first step to develop markets for structural applications and decking.
Densification increases the strength of wood in relation to its dimensions. Wood is compressed under heat into a smaller, denser piece of wood that stronger. Densifying poplar by 217% increased bending strength by 171% and stiffness by 230% (Sözbir et al 2019). However, the densified wood is subject to “spring-back” (also called “compression-set recovery”) when the wood is subsequently exposed to moisture (Cai et al. 2013). Increases in strength and stiffness in Eastern cottonwood (Populus deltoides) were reported to be proportional to the increased wood density resulting from densification (O’Connor 2007 as cited in Esteves et al. 2017). However, densification alone does not improve decay resistance for poplar (Kutnar et al. 2011 as cited in Esteves et al. 2017).
Combined densification and thermal modification
Densification combined with thermal modification has been trialed on poplar in an attempt to increase durability while retaining its strength properties. Thermal modification of timber at temperatures sufficient to impart biological durability results in reduced strength (Esteves et al. 2009), whereas densification improves strength, so if combined could result in a structural product.
Fang et al (2011) found that the higher the temperature and duration of the thermal treatment, the lower the level of compression-set recovery in densified Populus. Compression-set recovery was almost completely eliminated by subsequently thermally modifying the wood using an Oil Heat treatment (OHT) above 200°C (Welzbacher and Rapp, 2007 as cited in Anshari 2012).
Bending strength and stiffness were also higher if heat treatment followed densification. Pine wood densified by 70%, then heat treated at 190°C, was stronger and stiffer than untreated wood. (Esteves et al. 2017). Gong et al. (2010) also reported that both hardness and strength of densified, then thermally treated poplar was increased from untreated wood. Esteves et al. (2017) found that densification followed by heat treatment produced a much lower compression-set recovery ("spring-back") than heat treatment followed by densification. Sözbir et al. (2019), however, found that heat treatment before densification of poplar produced similar mechanical properties to untreated poplar. It appears that more research is required to refine and optimise the process for commercial densified thermally modified structural poplar products.
DMDHEU (Dimethyloldihydroxyethelenurea) is a water soluble glyoxal resin that when impregnated in wood as an aqueous solution causes permanent bulking of the cell wall, producing a wood-polymer composite. Resulting properties include improved dimensional stability, surface hardness, density, stiffness and durability of the modified wood. This "modification" process does not utilise chemical preservatives, but the level of improvement in wood properties does depend on chemical loadings, which can vary from 15-30% weight percent gain (Militz et al 2011). Modification of solid wood is limited to permeable wood species that are easy to impregnate (Emmerich et al. 2017). Radiata pine has undergone limited testing for impregnation New Zealand, with only the sapwood impregnating well (M. Fortune, pers. comm). Poplar could be tested for impregnation of both heartwood and sapwood to assess its permeability. If the heartwood impregnates well, this could generate market opportunities for the wood, based on improved durability and hardness.
Posts and Poles
Despite poplar being lower in strength and density than radiata pine, treated posts and poles may have some market potential in New Zealand.
Pressure treatment of dry sawn timber with CCA salts has been shown to provide variable penetration (Williams et al. 1986), whereas Wilkinson (2000) reported that "CCA-treated poplar has been widely used for fence battens and gates".
Chrome-copper-arsenic (CCA) preservative treatment of air dried roundwood was found to be satisfactory (Williams et al. 1986). However, the contemporary method for preservative treatment of posts and poles is a two-step process that uses green (freshly harvested) posts and poles rather than the traditional method of drying before treatment. These are steam pre-treated under pressure to condition the wood, followed immediately by pressure treatment. This method is standard practice at Mt Pokaka Timber Products, Kerikeri, Northland, but has apparently not been assessed for treatment of poplar posts.
Noting that very little work has been undertaken historically in New Zealand and the sample size tested by Williams et al. (1986) was very small, their conclusion that poplar posts and poles have low strength, poor nail and staple holding, and preservation problems should be reassessed. Research should also consider contemporary solutions to these issues and Kawa, with its high wood density, should be trialled as preservative-treated post products.
Next steps
A full body of research is required to unravel the full market potential for poplar timber products. For soil conservation plantings to scale up to the level required to significantly reduce production of hill country sediment in Northland, utilisation of the wood being produced by soil conservation trees is essential. This research focuses on high-value sawn timber products from Kawa poplar, including interior structural timber, thermally modified weatherboards and window joinery, hardened flooring and H4 treated posts and poles. Although this regional research project does not intend to resolve all the issues and test all the products described in this literature review, the intention is to undertake some testing to identify areas for future work so that industry, territorial authorities and stakeholders can consider options to unlock the market potential for poplar timber.
Disclaimer: The opinions and information provided in this report have been provided in good faith and on the basis that every endeavour has been made to be accurate and not misleading and to exercise reasonable care, skill and judgement in providing such opinions and information. The Author and NZFFA will not be responsible if information is inaccurate or not up to date, nor will we be responsible if you use or rely on the information in any way.
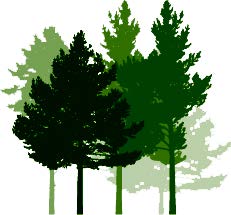