Progress in mechanised tree planting
Carol Rolando and Claire Stewart, New Zealand Tree Grower August 2024.
Even with the low-skill entry level and camaraderie which is part of planting crew culture, it is not a job for the faint-hearted and people prepared to do hard manual work are becoming scarcer. Owners of large and small-scale forests are experiencing increasing difficulty in finding reliable planting crews, and inevitably some of the owners of the largest forests have begun looking at mechanised alternatives.
The method so far has been for some management companies of large forests, and one major silviculture contractor, to import machines from overseas and test them in their own operations.This, and the alternative of developing bespoke machines here, are expensive and risky.Those who have taken the plunge and invested in planting machinery are committed to innovation. Several of these companies are partners in the Forest Growers Research Precision Silviculture Programme, working together to evaluate and develop their mechanical planting systems, as well as sharing lessons learned with the broader forestry community.
The M-planter and PlantMax
Mechanised planting has been increasingly tested and evaluated in many other countries, notably Brazil,
Finland and Sweden, where forestry is on different land types than in New Zealand. Before 2018, planting operations on cut-over sites were carried out only using manual labour.Then in 2018,Timberlands Ltd imported a machine called the M-planter from Finland to see how it worked in Kaingaroa Forest. Subsequently, two of New Zealand’s other large corporate forest owners, Manulife Forest Management (NZ) Ltd and Rayonier- Matariki Forests, have also tried the M-planter in central North Island forests under a range of conditions.
More recently, Hawkes Bay-based Pan Pac Forest Products Ltd imported a Swedish PlantMax planter, a very different machine.The first trials with the PlantMax began in Hawkes Bay in July 2023.
As both these machines are new to New Zealand forestry, the Precision Silviculture Programme saw an opportunity to work with the machine owners to study performance of the machines, contribute to their development and adaptation for New Zealand conditions, and look for ways to integrate mechanised planting into forest-growing.
Evaluating the M-planter
The M-planter is a Finnish machine, first produced in 2006. It comprises a planting head attached to a hydraulic boom mounted on a 25-tonne excavator base machine.
The M-planter operator spot-cultivates the site and then plants individual seedlings into each spot. More sophisticated versions of the machine include the ability to slash rake, spot rip and mound, plant, fertilise, apply hydrogel and also water seedlings at planting. The sole machine operator is responsible for manually loading containerised radiata pine seedlings into a cassette which sits on the planting device.
Working together with H A Fear Ltd, a silvicultural contractor who operates the machine, Timberlands began testing the M-planter in winter 2018 in cutover sites. They quickly identified various modifications needed to make the machine suitable for New Zealand conditions. These included the ability to spot mound, which has enabled site preparation and planting to be combined into a single operation. They invested in two more machines in 2019, and further modified them with adaptations to improve their ability to apply fertiliser and hydrogel to each seedling at planting.
The M-planters have been used in the Kaingaroa Timberlands forests every winter since they were introduced. Although only used in a small part of the forest, they are now considered in planning planting operations with their main attribute for use in Kaingaroa being the ability to spot mound and plant simultaneously.
Back to manual
Manulife Forest Management (NZ) Ltd started using the M-planter in Kinleith Forest in 2020 and planted approximately 100 hectares every year over the past three years.Their trials included attempts to increase the number of trees planted each day as a way of reducing costs.
Although they were successful in increasing planting rates from a starting rate of around 800 trees a day up to 1,350 trees a day, planting quality declined at the higher planting rates. The company reverted to manual planting for the 2023 season because they could not see the productivity of machine planting improving substantially in the short term.
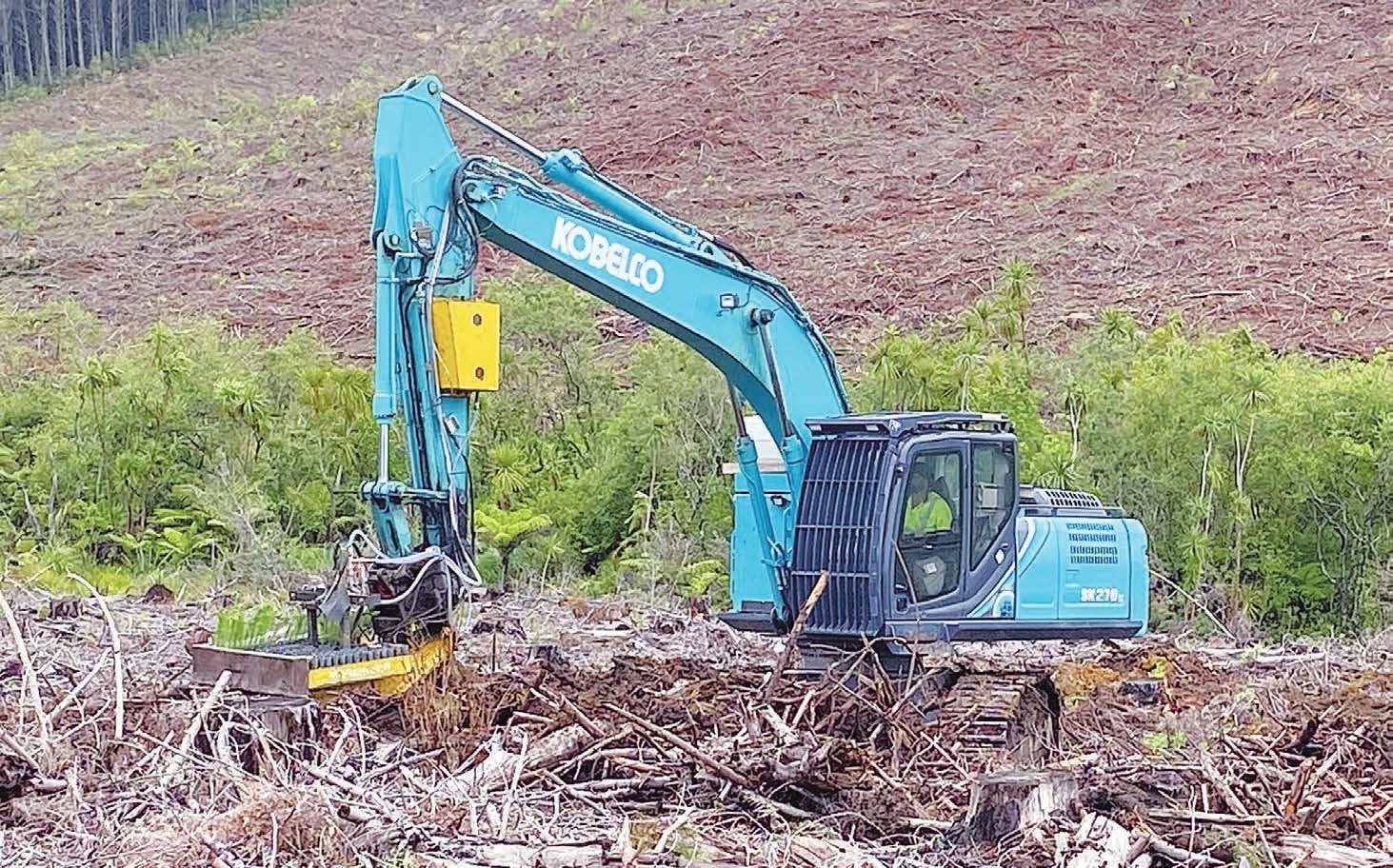
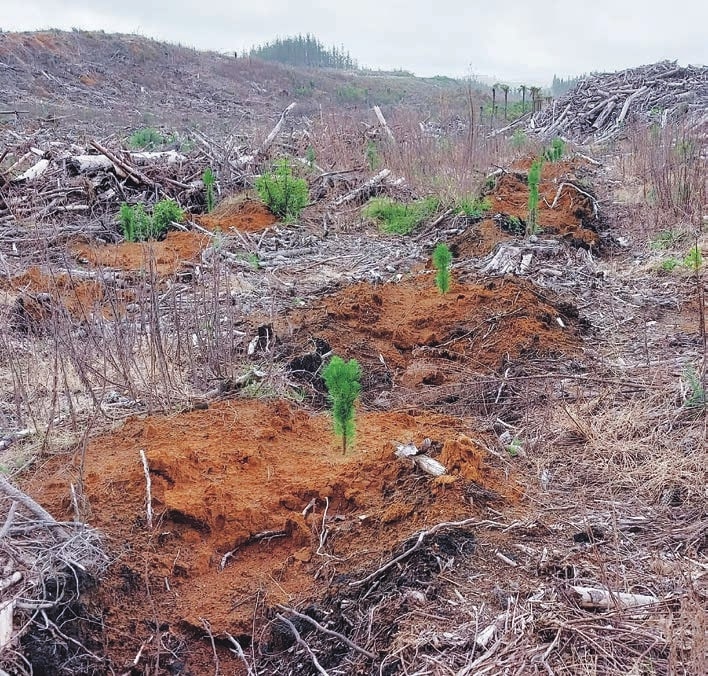
Rayonier-Matariki Forests have also used the M-planter because the company was particularly interested in extending the planting season using hydrogels. So far, they have planted two small trials on contrasting sites, learning many lessons along the way about the challenges on heavy, wet clay soils.
Reviewing the productivity
In 2023, a team from Scion worked with forestry company staff to review the operation of the M-planter. This review summarises results from operating over five planting seasons in terms of –
- Productivity across different land preparation and site conditions in comparison to manual planting
- Planting stock quality and storage
- Adaption to improve performance.
Some practical conclusions included the need for improvements which will increase productivity while maintaining a high level of planting quality. Recommendations included requirements for adjustments of planting head pressure and the post-planting side compaction panels for planting on different site types. Heavy soils can cause problems by blocking the planting tube. Root plugs need to be well-consolidated or they can disintegrate, and shorter sturdier seedlings appeared to give the best results. It was found that seedlings are at risk of deteriorating on site before planting, so better seedling handling is needed to avoid this.
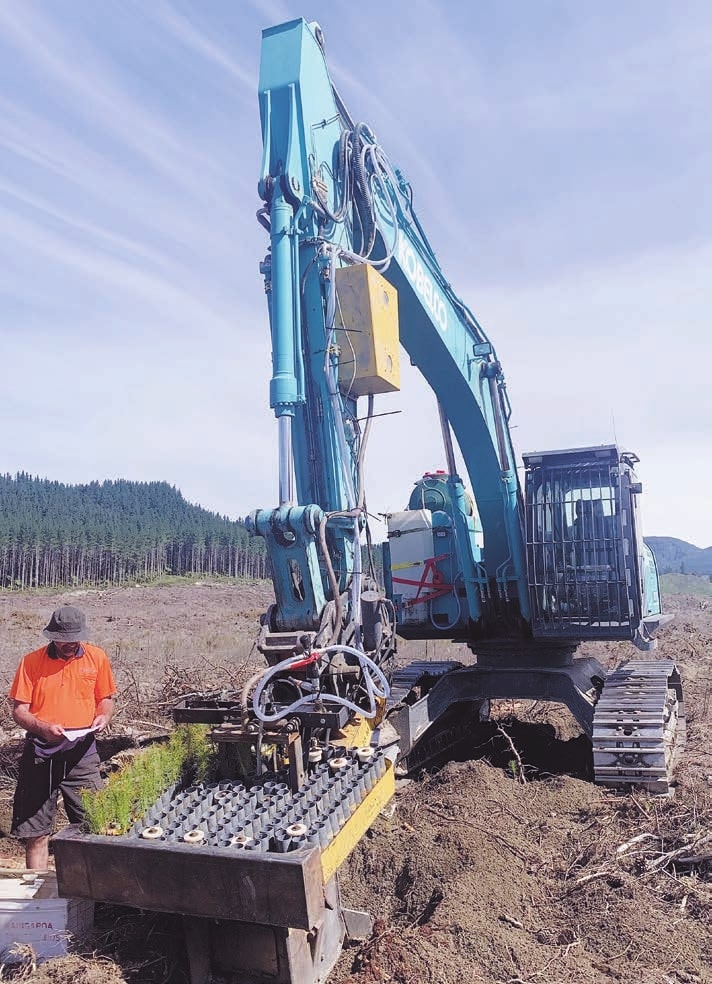
Finding the right operator for the planting machine is also important. M-planter operators must be prepared to get out of the cab quite frequently, handle seedlings carefully and be conscientious about planting quality while still achieving productivity targets.
Cost-effectiveness
As well as practical lessons and operating recommendations, the review includes economic analyses of operating the M-planter, especially when compared to manual planting.The hypothetical analyses were based on planting 1,000 hectares over a planting season of three to four months.This could reasonably be achieved by a 10-strong manual planting crew or would require 10 M-planters planting 1,000 seedlings a day.
A basic comparison of planting costs, excluding any costs for land-preparation, shows that manual planters are currently substantially cheaper than the M-planter. However, if land preparation costs are included, and this work can be done concurrently by the M-planter, then the comparative costs become closer.The most promising option economically appears to be where a combination of manual and machine planting is used. In practice, manual planters would plant the steeper areas and the M-planter would carry out land preparation and planting on the easier country because excavator machine planting can only be carried out safely on slopes of less than 22 degrees.
Striking the right balance between productivity in terms of trees planted each day and planting quality is vital for this machine to be considered a viable option. A sensitivity analysis based on performance to date revealed a current sweet spot of around 1,100 trees a day, above which the rejection rate increases and cost-effectiveness decreases. However, realistically the M-planter needs to plant at least 1,500 trees a day to be economic.
The cost-effectiveness will improve if the machine can be further modified to plant trees more quickly and correctly in the variety of site types likely to be encountered in New Zealand forests. Additional trials with Aspect Forestry Ltd and several forest companies in Nelson,Tasman and Marlborough for the 2024 planting season are aiming to do just this, to ensure we have fully evaluated the potential of the machine in a broad range of conditions.
The advantage forest owners see in having one or more M-planters is that planting can continue with a single operator even when a planting crew is unavailable. Having a planting machine provides security against perhaps increasingly frequent labour shortages.
Evaluating the PlantMax
Pan Pac Forest Products Ltd, based in Napier, imported a PlantMax machine from Sweden to evaluate its performance in Hawke’s Bay conditions.This machine is a radically different design from the M-planter, and under ideal conditions in Sweden it has planted up to 2,800 seedlings an hour. In other words, a complete game-changer if it can operate at this level on our varied terrain.
An Eco log 574E forwarder tows a second wheeled planting machine. Usually crewed by two operators, the combination has a scarifier on the front and two planting arms at the back, capable of planting a tree every three seconds. It can record seedling location and other planting information and has the potential to become part of an overall precision tree establishment and management system.
First trial planting
In winter 2023, Pan Pac embarked on large-scale evaluation with the PlantMax on contrasting site types in Hawke’s Bay.The team started out planting on easy, flat-to-rolling land on a first rotation site near Tutira,
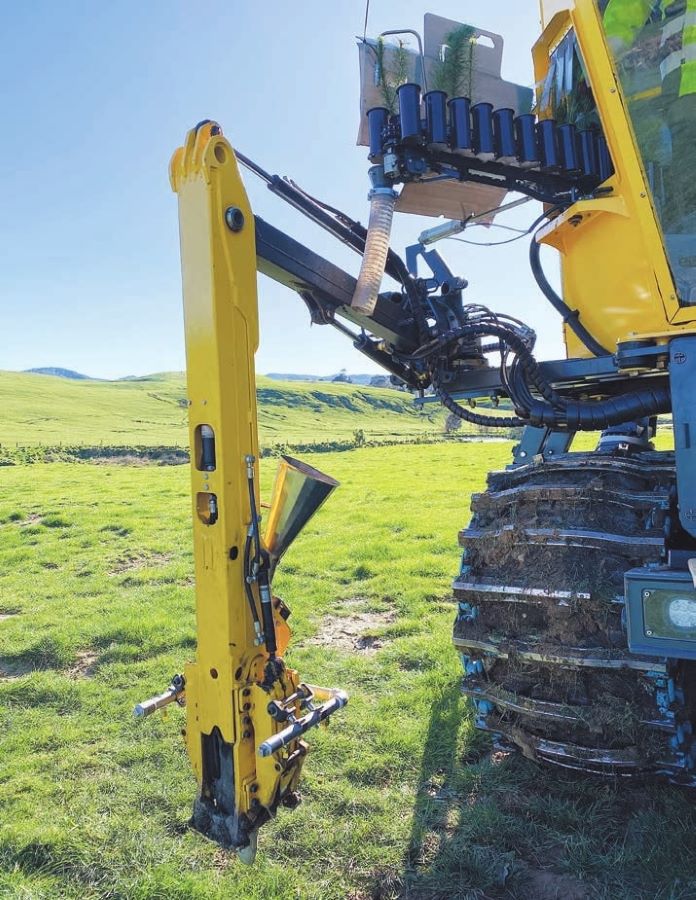
Mechanised tree planting north of Napier, then moved on to more complex cut-over terrain in Gwavas Forest. Here, initial blocks selected for planting were flat with low levels of slash, with the machine then moving to progressively more complex land which was steeper, then with gulleys and higher levels of slash as the testing progressed.
Assessing the operational performance of the machine included benchmarking stocking density, planting speed, planting quality and tree mortality after planting. Scion has established trial plots to assess the performance of seedlings planted with the PlantMax on the two contrasting sites.These plots are being compared with manually planted plots in each case.
As with the M-planter, the PlantMax only uses containerised stock. However, investigation into the ability of the machine to plant bare-root stock are under way. Future assessments will provide more conclusive results about how well the machine performed and provide better insights into planting stock specifications for planting.
Planting rates
Over the trial period of 35 days, the PlantMax was able to achieve an average planting rate of 1,800 seedlings an hour, with up to 2,100 seedlings an hour on the ex- pastoral site and 1,500 seedlings an hour on the cut-over. In the cut-over, the scarifiers worked well in eliminating the need for an additional operation to prepare the land for planting, significantly reducing total planting cost.
However, there were many problems. At the planting speed achieved on the ex-pasture site, the tree-feeding operator had trouble keeping up with the machine. In addition, while a high planting rate was achievable, this was limited to certain land types, with an average of 45 per cent not accessible. One of the main challenges at this stage appears to be the base machine’s inability to manoeuvre efficiently around gulleys, headlands and small obstacles, resulting in significant gaps left across the planted block.These then need to be manually planted. Pan Pac are already looking at a different type of platform for the planting machine so that it can cover a greater proportion of planting sites.
Tempting benefits
While it is still early days for testing modern mechanised planting technology, the perceived benefits are tempting enough to encourage large-scale forest owners and contractors to take the leap into investigating planting machines.These owners and operators who are committed to investing in trials are well aware that manual planting remains a cheaper option in the short term.
The M-planter and the PlantMax require substantial modification before they can perform optimally on rugged sites and planting conditions. Once full commitment to either, both, or even alternative machines by the industry occurs, the next challenge will be to develop the skills and systems required to optimise their potential.
The best-case scenario for the two machines working in New Zealand at the moment appears to be combining machine and manual planting. If these dual systems can be refined to become efficient, it appears that a significant change in large-scale planting practices is on the horizon.This is especially the case with the PlantMax, thanks to its rapid planting speed.
This change will be a critical part of the modernisation of the forestry supply chain. It starts with nursery production of the best forest genetics, precision planting and management, to harvesting and processing, and the evaluation of results and productivity from different systems and sites.
Levels of mechanisation in forest harvesting have increased dramatically, so the industry has focused training new entrants on operating machines. As a result, fewer people are being trained in safe manual felling.
Skilled chainsaw operators are becoming a precious commodity and by implication, the challenge for the industry will be to continue to train enough skilled manual planters to work alongside planting machines.
Only for large forests
In the short term, only owners of large forests and the largest planting contractors are likely to take the risk of investing in importing machines or building their own machines. For those growing smaller forests, mechanised planting appears to be some way off, and in the foreseeable future, far less likely to stack up economically than manual planting. Even just the cost of transporting mechanical planters to site, especially if the block is relatively small, would be a substantial addition to regular manual planting costs.
In the longer term, if planting crews become scarcer and machines potentially more common, then the prospect of small-scale growers having no alternative but to use planting machines could become a reality.
However, in the short term this is very unlikely with manual planting continuing to be the dominant planting method while machines are evaluated.With the range of planting machines coming on to the market overseas, its unlikely to be a one-size fits all solution. It is more likely that there will be a range of options to choose from depending on the area to be planted, the terrain type and the planting precision required.
The Precision Silviculture Programme is exploring other technology solutions to help make the job of tree planting more streamlined for owners of smaller forests. This includes modification to planting spades which enable tree location and other data, to be obtained and recorded at the time of planting. It will still pay to keep your planting contractor on side for some time.
Carol Rolando is a Senior Scientist at Scion and leads the Planting and Establishment theme of the Precision Silviculture Programme. Claire Stewart manages the Precision Silviculture Programme.
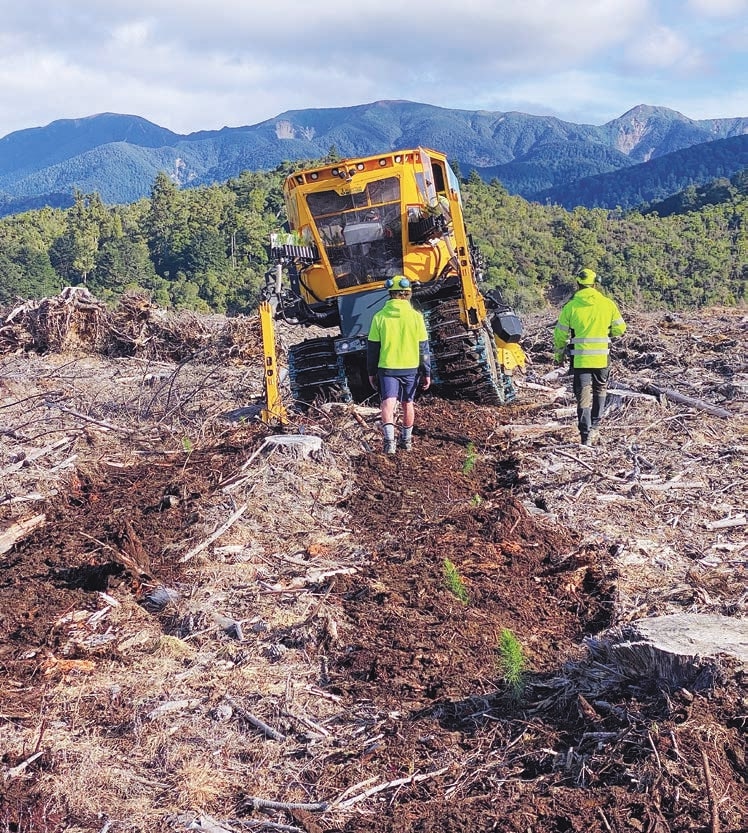
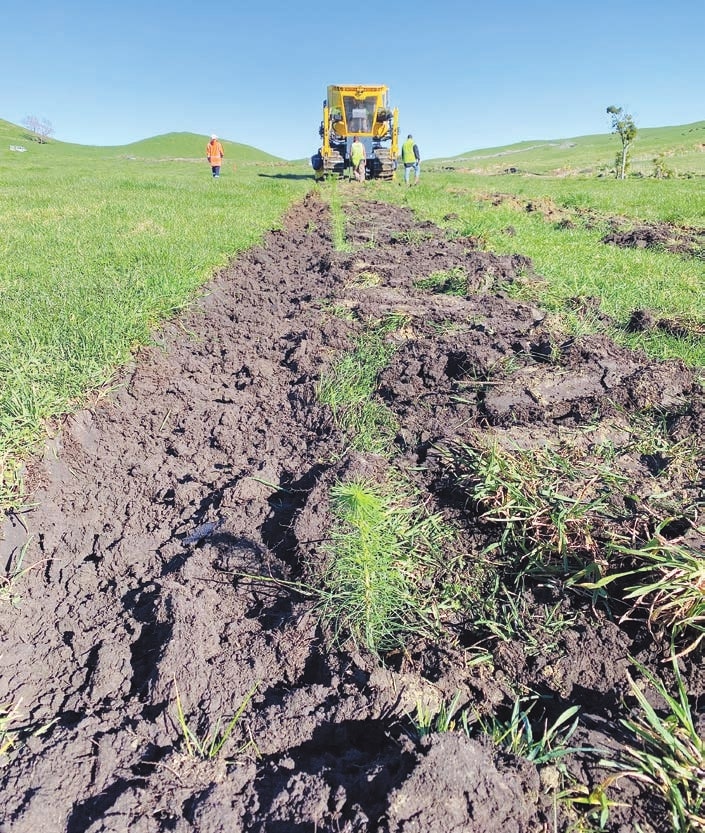
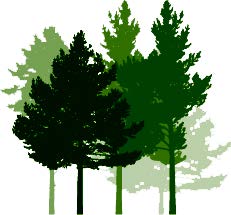