Lindsay and Dixon’s beech harvesting operation
Ian Campbell, New Zealand Tree Grower May 2010.
The day started well with an address to the conference at breakfast time from Bernie Lagan, co-owner of Lindsay and Dixon. Bernie outlined to us the type of operation we were about to see. It became apparent very quickly that this was no simple organisation exploiting our native forest, but a well tuned, carefully managed operation harvesting the silver beech forests of western Southland in a sustainable fashion.
The conference was again an excellent event and all those who made the journey will have been pleased that they decided to go to Invercargill. Due to the tight time constraints there is only one field day report in this issue, but the rest will be included in the August Tree Grower, something to look forward to. The theme of the conference was trees other than radiata pine and this was managed very effectively, with hardly a radiata pine seen except in the distance.
The forests being harvested are predominantly silver beech, with small volumes of mountain beech, kamahi, rata and other podocarps. The forest is held by the Waitutu Corporation through a ‘profit a prendre’ with the crown. All the areas being harvested are second growth forest which had been clear felled in the early 1900s. FSC certification Lindsay and Dixon has put considerable emphasis on obtaining FSC certification and this was a recurring topic throughout the day. They regard certification as another overhead, not something that necessarily adds value to the product. But are they are sure that without it they would not have obtained some contracts, such as making the Beijing Olympic torches or supplying panelling for the Supreme Court in Wellington. They have spent around $600,000 on the certification process since 2004. This makes up about 2.5 per cent of the cost of a finished product which brings in an average of $900 to $1,000 per cubic metre of wood sold.
We were all very impressed with the level of skill demonstrated by everyone in the company. The process starts with the felling and extraction of trees from 11,500 hectares of beech forest in several different blocks in the Longwoods region of Southland. Here the skill is first to choose the right trees and then fell them in such a manner that the least damage is caused to the surrounding forest. The forestry workers are proud of their job and work from computerised cutting lists showing the sizes of trees to extract that will maintain the forest. They record all their activities for later entering into a programme the company has developed modelling the various forests. Small coups or clear felling small areas at a time were tried but now the technique is to carefully extract selected trees taking into account the need to create light wells for regeneration. There was considerable discussion among the group on the merits of the two techniques − it would not be a farm forestry trip without it. An area of forest can be revisited for further log extraction in 15 years.
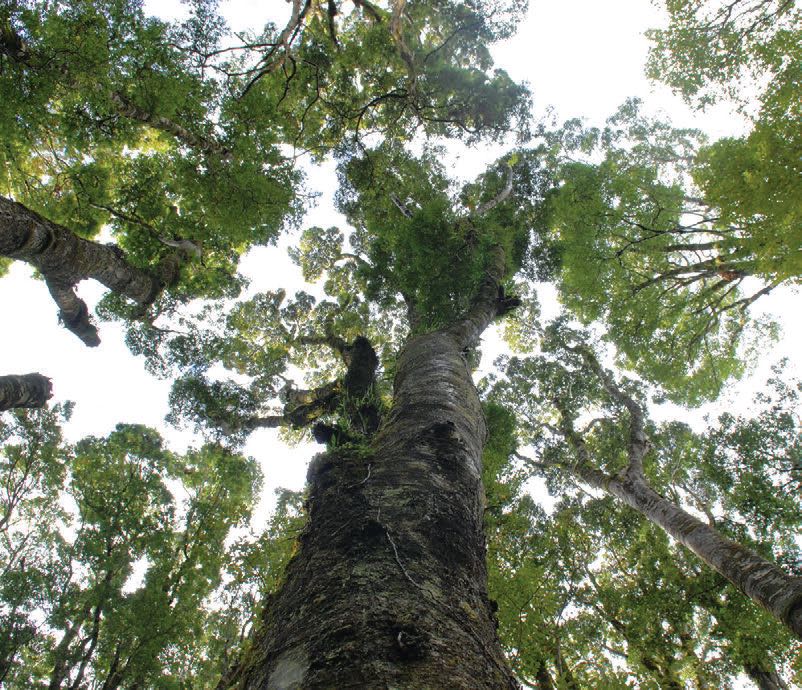
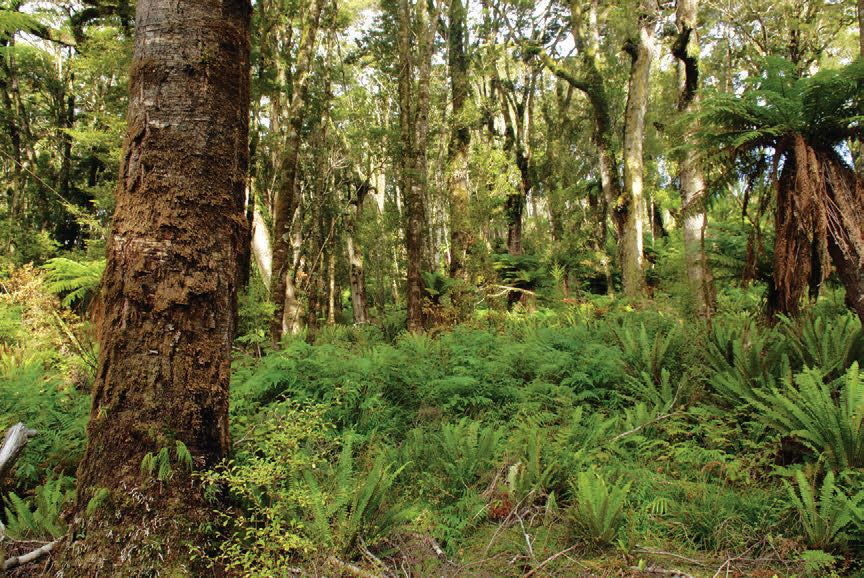
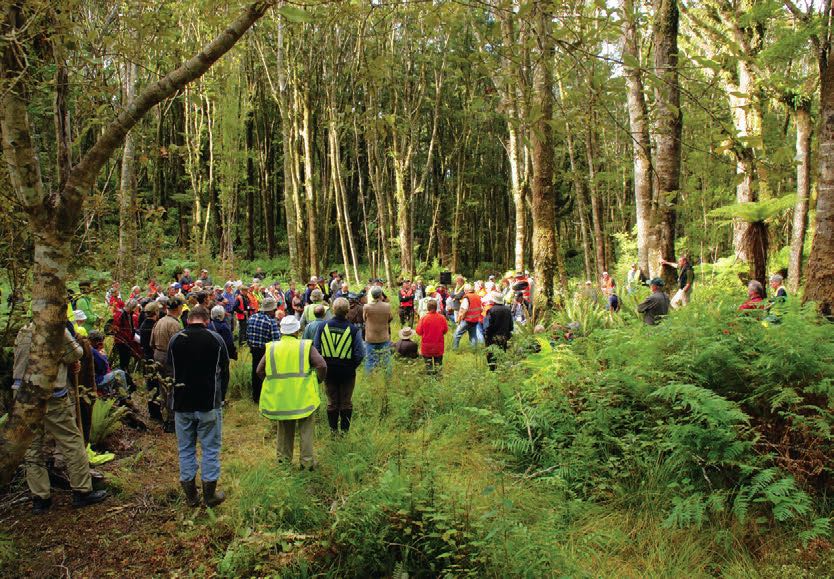
Forestry roads
The nature of the logs being extracted rules out helicopter logging as uneconomic so all timber is removed on temporary forest tracks. Initial roads in the forest were traditional cut- and- fill construction but this caused too much environmental damage. Now a narrow track is cleared and a layer of top course put down for the trucks. This technique has cut the cost of roading from $30,000 a kilometre to $15,000 a kilometre. All streams have temporary culverts installed or corduroy crossings established. It has been found that normal rubber tyred machines in the forest caused too much disturbance of the forest floor, so now low ground pressure high – arched tracked machines are used. One of the impressive aspects of the company is their willingness to modify techniques to cause the least damage possible to the environment.
Low impact forestry
Discussion in the forest was led by MAF and the regional council who are closely involved in monitoring. Gary Morgan, the representative from Environment Southland, and Allan Tinnelly from MAF spoke highly of the operation.
Allan commented on the positive low impact the method has in the forest and complimented the skilled team who minimised damage and were excellent to work with. The company has developed and signed a memorandum of understanding with Environment Southland. This covers culverts and bridges, water quality monitoring, and bird monitoring. The results have been very good and well below the acceptable targets. There is plentiful invertebrate life in the water along with eels, freshwater crayfish and various galaxids. Murray endorsed the comments, noting credit must go to the gangs who work in the forest who have a real sense of pride in the bush and with what they are achieving.
Milling
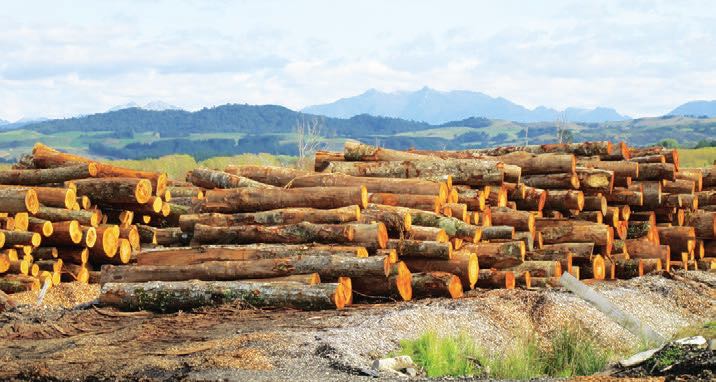
A stockpile of logs to cover at least 10 days of mill operations is maintained at the mill site. This means about 500 cubic metres are in the log pile at any time. No sorting of logs is done in the forest and the logs we saw were all of reasonably uniform quality and up to 70 cm in diameter. They are apparently about 80 years old when harvested. The mill is a conventional type with a primary band saw squaring up the logs and a circular saw completing the job. As always in milling operations, the skill of the operators’ decision as to just how logs should be treated has a large effect on the efficiency of the operation. Visitors to the mill are well catered for with an overhead gallery giving a good view of operations and no restrictions are made on photography. The timber coming off the sorting table was consistent in quality but with a marked variation in colour from pale to reddish brown. There were some signs of damage from pin hole borer but the company cleverly markets this timber as ‘pinhole antique’ and it is regarded as a premium product.
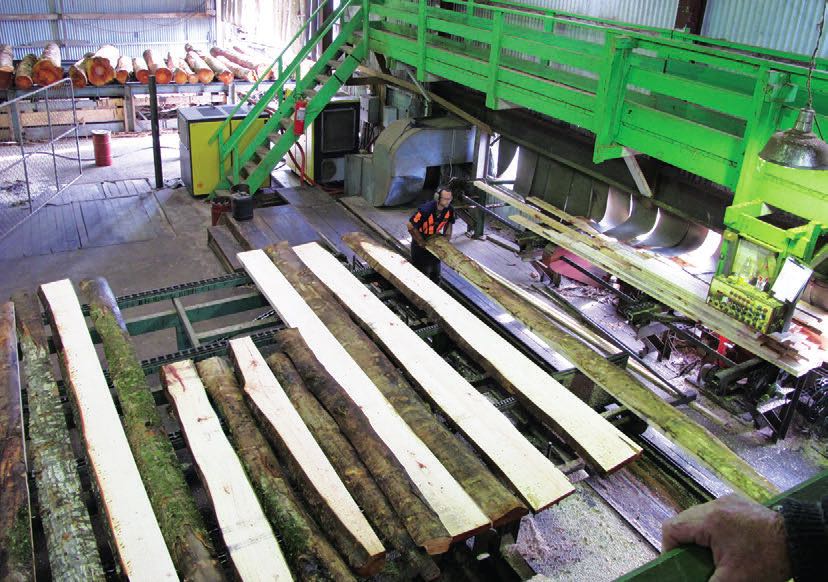
Drying and processing
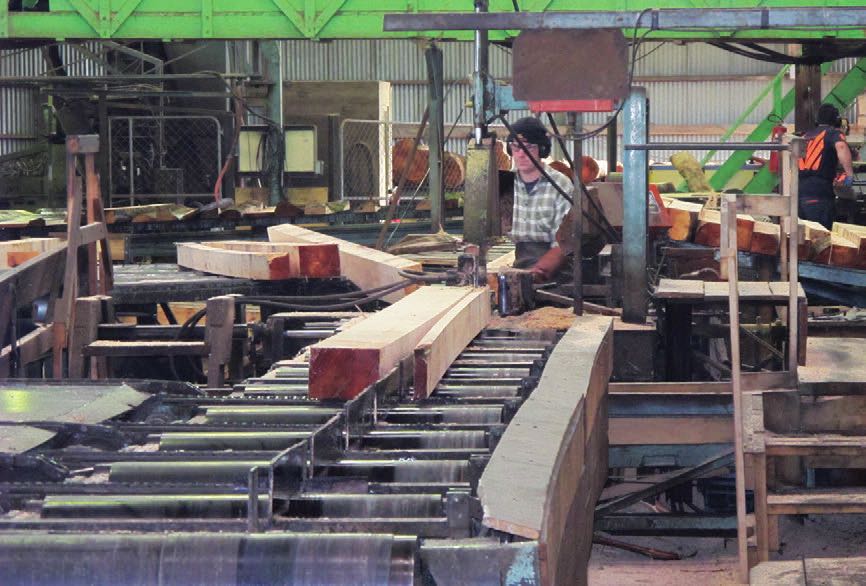
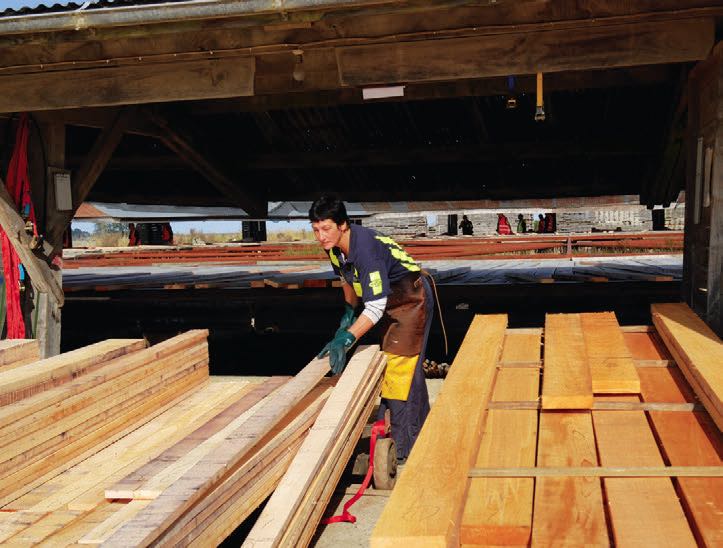
The timber from the mill is moved across the road to the kiln drying plant and then on to be processed into various products. The heat for the kilns is produced from the waste as the timber is further processed. The sawdust and shavings are sought-after by dairy farmers for cows to stand on and others requiring fuel for boilers. Some of the end product is sold as cut to length planks for joinery firms. This timber is very well prepared for shipping in packets wrapped in plastic bearing the firms logo and is sold as maple beech or cherry beech. Maple beech has an attractive honey colour and subtle grain patterns while cherry beech is the same timber put through a steam process that imparts a very attractive pink blush to the timber. This colouring permeates to the centre of the planks and is permanent. A large market for the firm is in producing laminated blanks for drawer sides in joinery of all types. It is critical for this application that the timber is stable and free from blemishes and this is achieved by precision sawing boards of 40 mm by 30 mm into lengths, laminating them into wide boards and then re-sawing them to the desired dimensions. As with all processes the laminating is done very skilfully to match grains and the resulting joins are barely visible. Other products in demand are flooring and wall panelling.
Widgets
The company has a section it calls its widget division where a variety of small items are produced. The ones we saw were broom handles and meat skewers but up to forty lines have been made in the past. The broom handles are made by feeding a flat board through moulding machine with semicircular shaped knives top and bottom, the resulting round sections are then rounded at one end and sanded in specially designed machines. During discussion at the end of the factory tour questions were asked about the profitability of the various stages and Bernie pointed out that while they have cost centres no part of the operation stands alone and that all aspects from obtaining certification to sanding end product contribute to the profitability of the company.
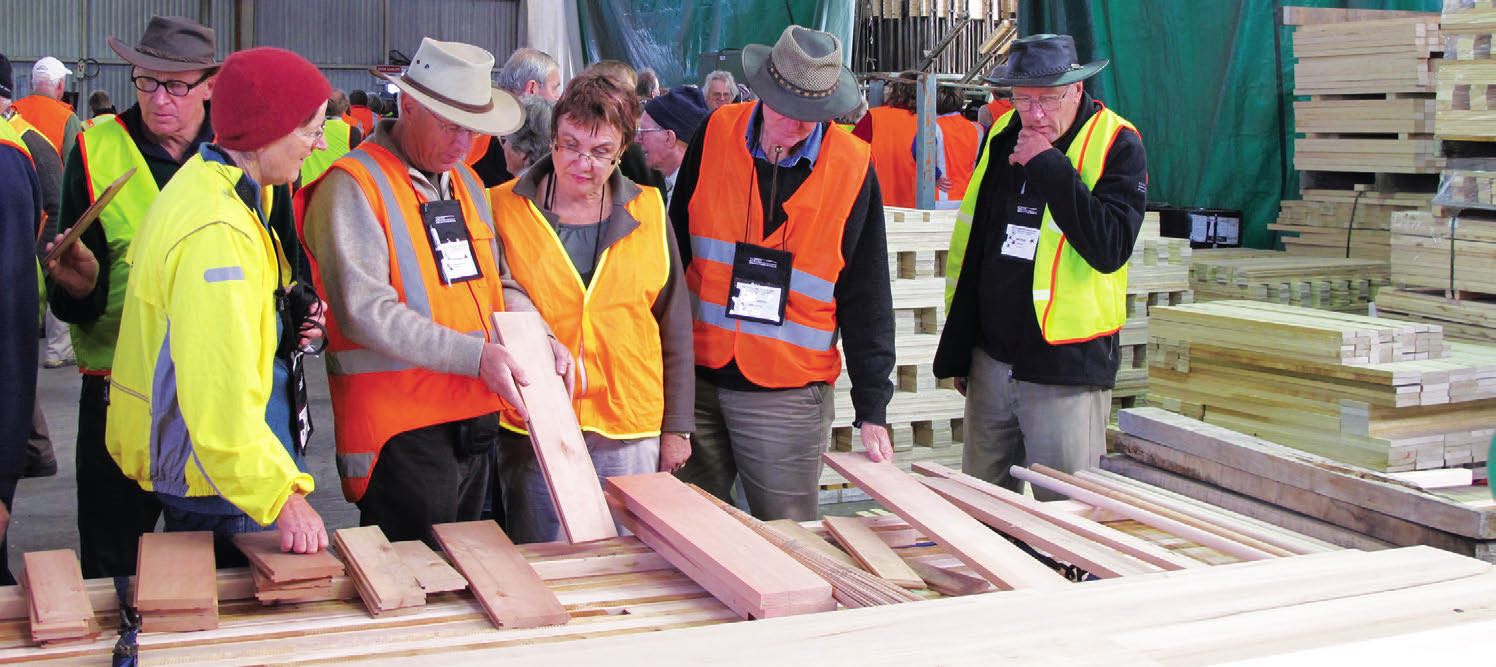
Successful enterprise
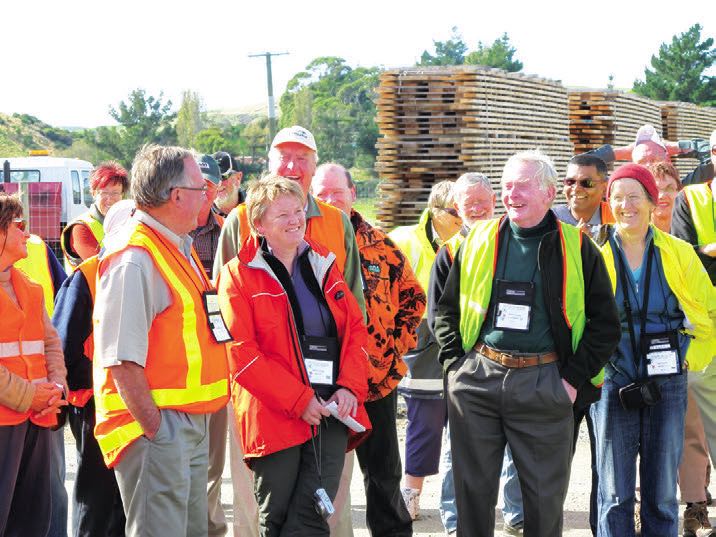
While reluctant to be specific it seems that the forest owners receive returns above that to be expected from conventional radiata forests. It is obvious that the enterprise contributes significantly to the Tuatapere community by employing 50 skilled staff and using other services. Other questions related to the ability of the company to expand its operations to other areas, but this is not needed as they are only using about half the amount of timber judged sustainable by MAF. Other aspects of the day’s tour included discussions on the effect on the Waiau River of water being diverted to West Arm as part of the Manapouri power scheme. The impression given was that there is local regret at the effect on their environment but it is better to look forward rather than back. So they make as good use as possible of the money Meridian pays as some recompense for the loss of water flow. There is currently an innovative scheme in progress to create whitebait breeding ponds at the estuary.
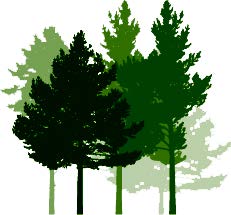