My trees have grown up – what should I do?
Peter Gresham, New Zealand Tree Grower November 2012.
This article is aimed at foresters who are contemplating managing their own harvesting and marketing. It is not advice about how to proceed or when to sell, rather it is a checklist for the things that need attention when you have arrived at the harvest stage. I draw on my experience in harvests for the past 20 years. Any organisation I have been involved with has always worked through a professional manager, but I have picked up information which I pass on for the DIY forester.
I am a self-confessed amateur in the field of plantation establishment and management. As one of the earlier people to promote forestry as an investment, I drew together a group of investors who funded the establishment of commercial plantations totalling about 2,000 hectares in the Wanganui area. I have harvested trees every year since then, starting in the monumental year of 1993, with virtually all areas harvested being replanted. In 2004, the withdrawal of Tenon from harvest management in the southern North Island, prompted me to start a harvesting and marketing company which has grown steadily since then.
The nice thing about growing trees is that there are a number of certainties encountered. One is that they will take about 30 years to mature and another is that you only cut them down once. In addition, once you start the harvest your trees will disappear rapidly, at about half a hectare each day, so plan your harvest well in advance and negotiate all the pitfalls before your contractor starts.
Suggested checklist
If I was to list all of the things needing attention before a successful harvest can begin it would look like this −
- Draw up a harvest plan showing all planned roads and the skid sites they service
- Apply for and obtain a harvesting consent from the local authority
- Organise a market for the logs domestically and export
- Organise a logging contractor for harvest and road clearance or formation
- Organise a road construction contractor with appropriate metal resources
- Organise a cartage contractor
- Ensure that roads and skid sites are constructed well ahead of the main harvest
- Coordinate all contractors to ensure that logs are supplied to market as arranged
- Ensure that finance is arranged to cover initial costs before revenues begin.
A plantation harvest is no different from most activities – if you cannot draw it, you cannot make it. A well thought-out plan is essential for a successful harvest and can save thousands of dollars in costs associated with roading and skid sites. Not all harvesting projects will require consents from local or regional councils, but you would be well advised to check on this point once you are able to produce your harvest plan.
Never assume that the sawmills will take your logs or that you can export what you like, when you like. Domestic sawmills operate on negotiated timber, planned well ahead of time and you will need to negotiate for a place in their supply lines. Exporting also needs planning. Domestic prices are fairly stable, but returns from exports can swing widely and are affected by factors such as exchange rates and shipping freight. The regular market report in Tree Grower gives you plenty of background.
Log ranges
Your plantation is likely to produce a range of logs something like this.
- P grade – pruned logs with no knots, probably sold domestically but increasingly sought after by exporters
- S grade – structural grade logs with knots less than seven centimetres, for domestic sales
- A and B grade – industrial grades with larger knot sizes up to 12 centimetres for domestic grades
- A K, KI and KIS grades – all export grades
- Pulp grades – destined for local pulp mills.
You may be well advised to have your plantation surveyed by a specialist forester to produce an inventory of what can be expected in the way of grades and quantities. You will need this to meld with your contractor’s expected requirements
to give the guarantees of supply to local mills that they will need. The cost of this will vary according to the size of your plantation. As an example, a 10 hectare block might cost $3,000 to $5,000 to survey depending on the terrain.
It is unlikely that you will be able to sell all your domestic grade logs to one sawmill as most specialise in a particular log grade or specification. This means that you need to negotiate with a number of mills to place your logs, which is why it
is important to have a good understanding of the log grades your forest is likely to produce. A number of sawmills in New Zealand have gone into liquidation or receivership over the past few years, so you would also be well advised to verify the financial standing of any mill offering to buy your logs.
Logging equipment and contractors
When it comes to the most suitable logging equipment for your job the main problem will be the terrain − what are the slope factors involved. This is a very large subject, but in simple terms, where the ground is flat to easy then a ground-based crew will suffice. Steeper land will need some type of cable hauler equipment. Ground-based crews usually operate a bulldozer, a rubber-tyred skidder and diggers.
Cable haulers, which can be of several types, are usually supported by a variety of equipment, often including all of that noted for ground-based crews. Road clearance, or road lining as it is often referred to, along with skid site clearance and formation are usually carried out by a ground-based crew.
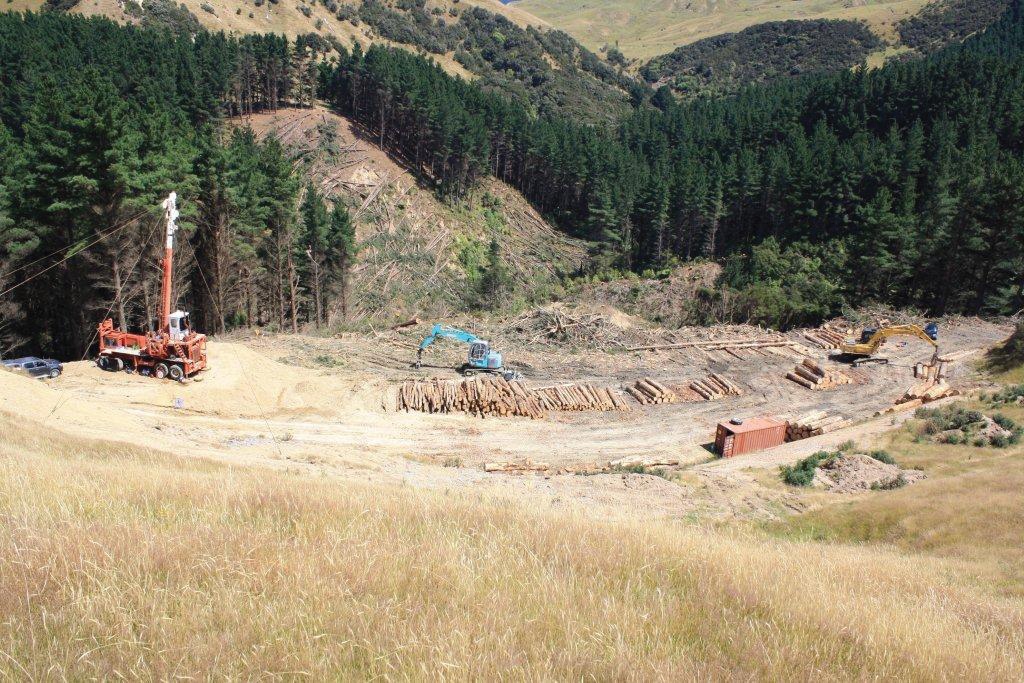
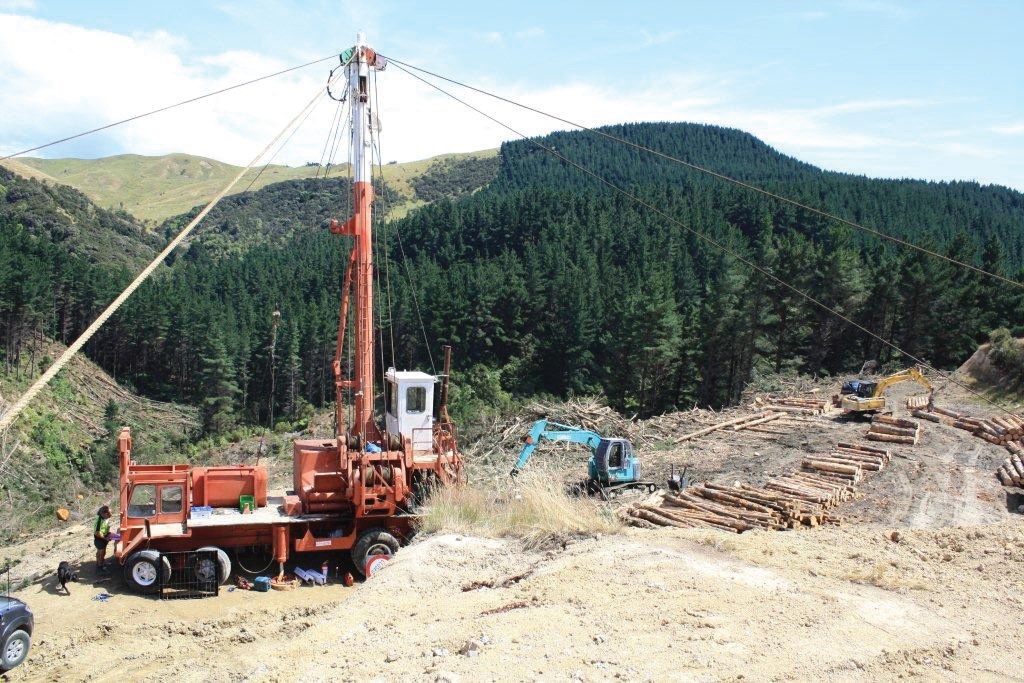
There will be a number of logging contractors working in your area and you will need to make arrangements with one who has equipment suitable for your job. Logging rates are negotiable and can vary from $18 to $25 a tonne for flat to easy land to $33 to $40 a tonne for steeper land or difficult areas. Some recent research has indicated figures of $50 a tonne or more for small forestry blocks on particularly difficult land. The attitude of a potential contractor towards the harvesting rate they will be prepared to work for will be influenced by the standard of roads and skid sites planned.
Similarly, there will be a number of transport firms set up for carting logs. Prices will need to be negotiated here as well with the same points regarding roading applying as for the logging. The cost of log cartage will depend on the location of the forest and the distance to the mills of choice or the export port. This can cover an enormous range, depending on the distance to the respective sawmills or export ports, but on average is between $20 and $35 a tonne.
An important point to remember when negotiating with these contactors is that they need continuity of work to be successful. They will therefore look closely at infrastructure and marketing arrangements make sure the project is well planned and likely to proceed smoothly.
Roading
The extent of road construction required will vary with the site and location and size of the forest in relation to the nearest public road. Significant savings can be made if there is access to a metal pit close to the site. Preferably, you will need to provide all weather access to the plantation for the carrier’s trucks. Roads of this standard must be extended throughout the plantation to service the skid sites where the logs will be stacked.
Costs of road construction will depend on the nature of the country, but expect to spend $30,000 to $60,000 per kilometre for all weather access roading and $3,000 to $10,000 for a skid site. Again, this is very dependent on the terrain and soil types of the area and shorter sections of roading will have a higher cost per kilometre.
It is advisable to construct roads and skid sites well ahead of their use to enable consolidation. The usual attention needs to be paid to drainage to preserve the roads in times of adverse weather. Road inclines over 15 per cent are to be avoided if logs are to be carried up them.
Coordination
For the forest owner who is managing their own harvest and marketing, I cannot stress too strongly the need for coordination of the various facets. The production from the logging contractor needs to be coordinated with the flow of trucks from the cartage contractor. The flow of logs from the plantation then needs to be coordinated with the schedule of supply agreed on with the mill owner or export agent.
A failure in any part of this supply chain could result in significant problems and delays.
Finances and replanting
A final point which needs to be made is that of financial provision. Pre-harvest roading and other work will cost money and might be carried out many months ahead of harvest. Even when the harvest starts there will be a time lag between receipt of revenue and commitments to pay contractors. Roading costs will depend on the job involved, but when it comes to harvest it would be wise, even in mid-sized forests, to make arrangements to fund $200,000 or more ahead of receipts.
I have not touched on the question of replanting which is another large subject. As you may have established your plantation in the first place, it can be presumed that you know your way about. In terms of financial provision you could work on a rule of thumb and set aside $1,000 a hectare to cover replanting. This will include pre-plant weed spraying and something for releasing and blanking.
Peter Gresham’s day job is chartered accountancy and he was the author of the submissions on taxation from the NZFFA to the Brash Committee some years ago.
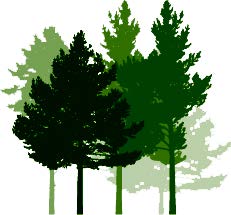