Keeping forest workers safe from harm
Kyle Ralfe, New Zealand Tree Grower November 2014.
Moutere Logging Ltd, a forest harvesting contracting business, has a simple philosophy − if our people are not in harm’s way, they cannot be hurt. Removing workers from hazardous tasks has been the motivation behind investing in developing mechanised technology. The result has been a reduction within the company in the annual rate of all incidents causing harm or potential harm from 220 a year in 2003 down to 50 in 2013.
The highest frequency of accidents or severity of accidents were on or around the skid site, breaking-out and tree felling. Breaking-out is where workers manually fasten felled trees with a chain to a cable system from the slopes of the hillside. The trees are then hauled to a landing before being processed into various log grades. Extracting logs which can weigh many tonnes in this unforgiving and often unpredictable environment can make this one of the most dangerous tasks in one of the country’s most dangerous industries.
The Falcon Forestry Claw is a motorised grapple carriage with a camera which operates on the cable harvesting system, and which virtually eliminates the need for workers breaking-out. The blue oblong carriage runs on a cable which can be lowered to the ground by slackening the tension, at which point the open grapple can pick up one or more felled trees. Once the grapple has a hold of the stems, the carriage is raised and then runs back up to the landing to with its payload. The amount of lift is determined by the slope, and because of this limitation it was initially expected that the carriage would only be used about half the time. As the crews became accustomed to the new way of working, they modified their techniques. Now we have eight cable crews associated with the company using the carriage almost 100 per cent of the time. That means that the risk to workers involved in breaking out is minimal.
Why is this carriage special?
The hauler operator, the worker who operates the cable and carriage system, runs the carriage out hundreds of metres away from the cab where the felled trees are to be extracted. Often the operator is unable to see directly where the carriage has to operate as it is over the crest of the ground.
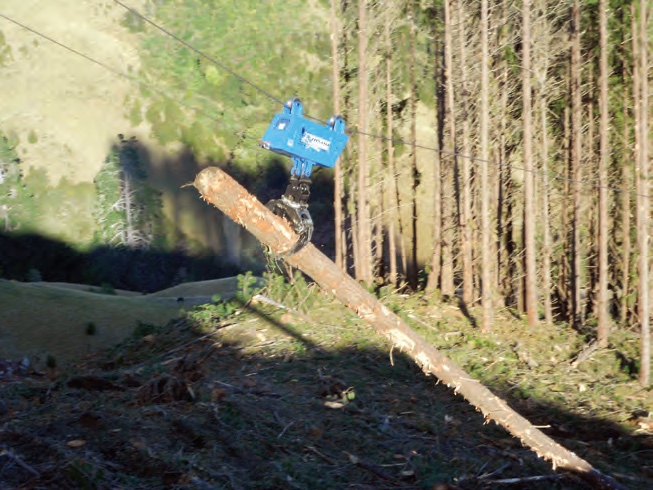
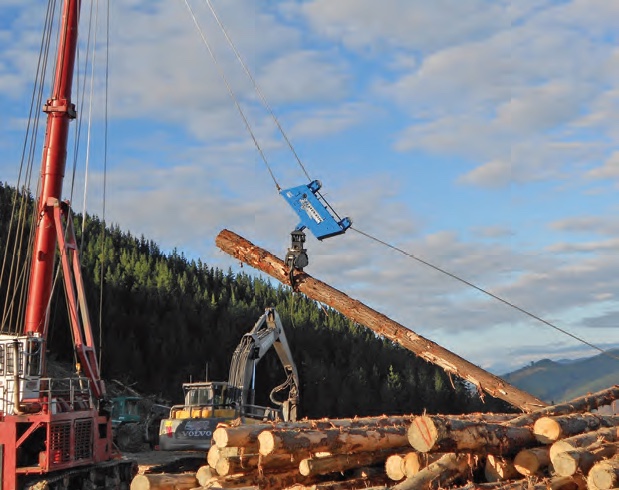
This is why the carriage was built with a fully weather-proof camera, which provides a live feed to a screen in the operator’s cab. The screen displays a clear view from the grapple’s perspective so that the carriage can be accurately manoeuvered to pick up the felled trees.
The operator is further helped with a GPS system which shows on the screen the distance from the cab, along with the elevation and coordinates of the carriage on the screen. All the information obtained by the GPS system can then be downloaded to a computer. This can then be viewed with cycle times for further analysis.
The camera has infrared capability for night vision, perfect for the short daylight hours of winter. The carriage also has two LED floodlights attached. These provide the hauler operator with extra light to see the felled trees when the carriage is higher off the ground.
Weight and fire suppression
The carriage is light enough to handle a large tree without overloading, with a maximum payload of eight tonnes. Fully opened the grapple from tip-to-tip is 2.2 metres and has a double knuckle allowing a 360 degree rotation. The grapple has a closing force of 27 tonnes which can be achieved in three seconds. A compact valve bank provides the hydraulics to control the grapple, which is powered by a diesel engine.
There is an on-board fire suppression system installed as a safety measure, which automatically triggers a fire extinguisher if the temperature rises above 110°C. The engine has a 12 litre fuel tank which means that with fuel consumption averaging nine litres a day, the fuel tank capacity is more than sufficient for a full day.
Safety benefits
The carriage has provided a number of unforeseen safety benefits for the crews. Interestingly, these benefits have been in another high-risk area of logging – tree felling. Before the carriage, tree fallers would need to fell trees in a direction which allowed the butt of the tree to be chained so it could be lifted easily, minimising breakage. Now they can fell trees on the face of a hill in the direction the trees are leaning, reducing the hazards and risks for the faller. This is because the hauler operator has more control with the carriage compared to using chains.
Breaking-out is a physically demanding task for workers. Tree felling all day is also physically demanding. To manage this, workers are rotated from these two roles with work on the landing, which is far less physical. With the introduction of the carriage, it is easier to monitor the fatigue of tree fallers when there is virtually no breaking-out to manage. One crew manager has said that since he has been operating with the carriage, his tree fallers can take more time to assess each tree before felling it and still fell the same number of trees each day.
Increased productivity
Productivity with the carriage has also been an evolution. Initially the carriage was as productive as a normal chain system. However the carriage cycle time is up to three times faster as there is no waiting for breaker-outs to run in, chain up, and then run back to their safe zone.
It was quickly discovered that if trees were bunched with an excavator then productivity increased significantly. This is due to the operator spending less time searching for trees, instead of returning to the same point as the previous drag, which is displayed on the screen. The operator can then grapple a number of stems neatly bunched, increasing the consistency of larger payloads.
Areas where an excavator can operate to bunch trees are limited by the land, with any slope over 30 degrees too steep. However, the company has also invested in winch-assist machines which allow excavators to operate on slopes up to 45 degrees. The excavators also have felling heads on them, meaning manual felling is minimised and bunched wood for the carriage is increased, maximising production. Simply put, it is safer and more productive.
Lighter model and more developments
As developments and understanding of the carriage progressed, a need for a carriage which could operate on smaller haulers and swing yarders was identified. A new lighter model has been developed and released. Two carriages have already been sold to a South Island contractor, and a third was exported to Chile’s largest forestry company, Arauco. This weighs 1,250 kilograms, which is 850 kilograms lighter than the original Falcon. It has a maximum payload of approximately six tonnes.
The carriage is constructed from high-tensile plate frame, which differs from the larger version’s medium-tensile box section. The hydraulic system was modified and the nine litre fuel tank feeds the engine. The grapple is smaller, at 1.8 metres tip-to-tip when fully opened, but it still has the same closing force of 27 tonnes over the same time of three seconds.
The evolution of the Falcon is set to continue. Currently a third arm on the grapple is in development. The purpose of this is to hold one tree while being able to pick up another one. It has been estimated that this will increase the productivity of the Falcon, in areas where bunching wood is not possible, by up to 30 per cent.
Using two carriages
Further development is in the pipeline for the system to operate as a tandem carriage. The aim is for it to work without needing to lower the skyline, a preference for some operators. This works with the main carriage held to a smaller carriage which runs along the skyline, and when the operator reaches the trees to be extracted the smaller carriage clamps to the skyline to hold it in place. Then the smaller carriage releases the main carriage, which is lowered via a separate cable, keeping the skyline raised. Once the trees have been grappled, the carriage is raised and connects back to the smaller carriage, which then unclamps itself from the skyline and returns with the payload.
A trial is scheduled to run the small carriage with the larger grapple. This will increase the total weight of the smaller carriage to approximately 1,500 kilograms, but allow the carriage to handle larger sized trees. If this trial is successful there will be a range of carriage options available, which can be tailored to meet the customer’s requirements, including wood type, equipment type and logging technique.
The cost and the value
The price of either the standard or light carriage is $115,000. The carriage replaces two men on the hillside and increases production by multi-shifting as the carriage can be operated in the dark.
Multi-shifting can be managed without extending the hours of all the crew. Only a hauler operator and another operator to clear the chute are required. Having two men start an hour or so earlier, or stay on in the evening, can increase production without incurring the full running cost of the operation.
It is recommended that a contractor buys the carriage rather than a group of woodlot and small-scale forest owners. The contractor would need to be familiar with it and potentially change the way they log. If an experienced contractor was expected to use it, it would be unreasonable to expect them to be productive and there could be other complications.
Currently there are approximately 20 Falcon Forestry Claws operating across various harvest contractors throughout New Zealand, with most of these operators contracted to the larger forest companies. However, as full mechanisation becomes increasingly more common, technology such as this will be more accessible for the woodlot and small-scale forest owners.
Kyle Ralfe is the Business Manager for Moutere Management Ltd who manage Moutere Logging based in Nelson.
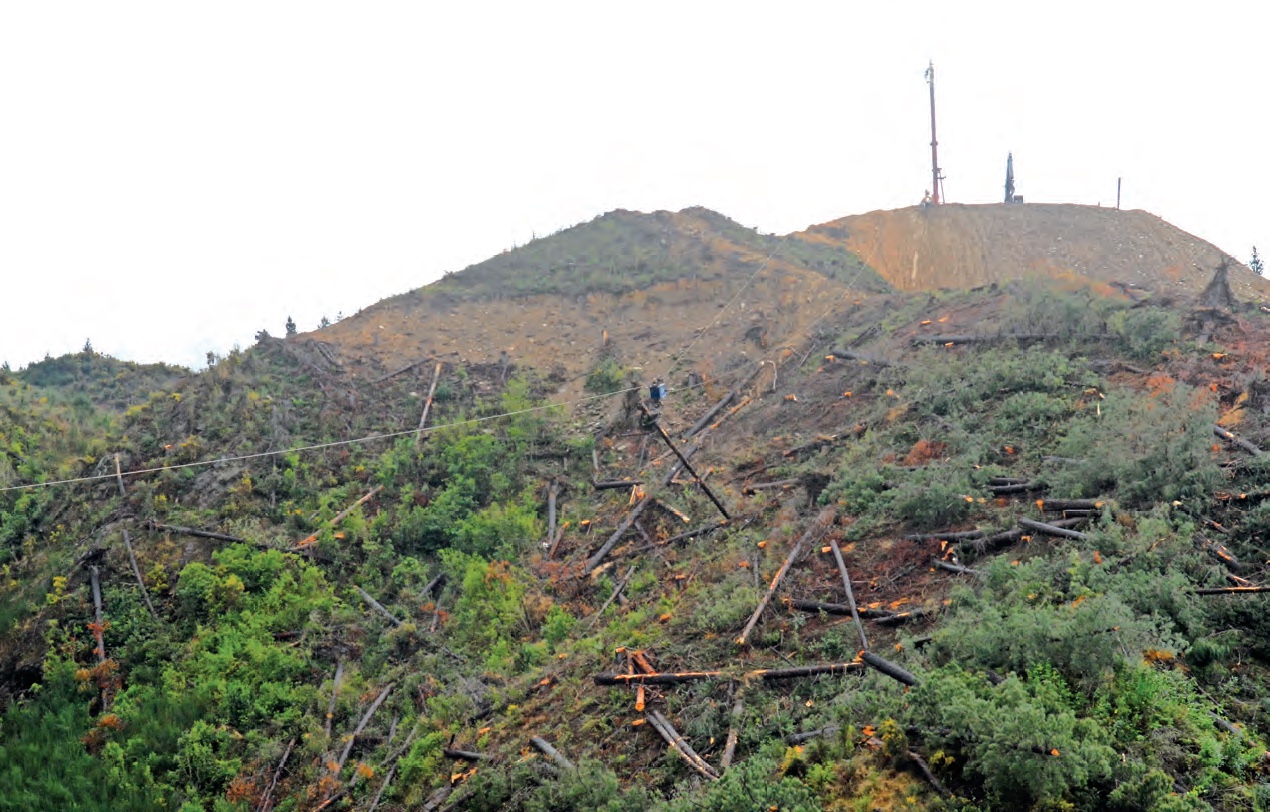
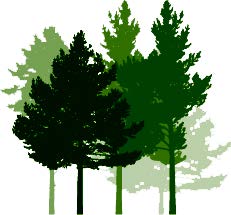