New harvesting technology for a safer future - Challenges of harvesting steep land
Keith Raymond, New Zealand Tree Grower November 2014.
The large areas of forest planted in the 1990s, now aged 15 to 21 years, are expected to reach harvesting age from 2018 onwards. As harvesting increasingly moves into these forests on steeper land and in smaller, more isolated holdings, the challenges of maintaining international cost competitiveness and safe operations will increase. Five years ago the New Zealand forestry sector and the Ministry for Primary Industries, or the Ministry of Agriculture and Forestry as it was then, identified steep country harvesting as the main bottleneck for greater profitability in forestry.
Worker safety is also a major problem. The forest industry has had a serious safety problem for far too long, with a long-term average annual fatality rate of five deaths a year and an annual injury rate each year at least one for every 40 workers. Steep country forests contribute about half of New Zealand’s total annual harvest volume and, according to the industry incident reporting scheme, about 40 per cent of forestry fatalities over the last five years.
More costs and more risks
Steep land harvesting has lower productivity, higher costs and higher risks than harvesting on flat land, mainly due to the higher work requirements and the difficulty of the steep land reducing the options for mechanisation. Cable logging costs are at least $10 a tonne higher than that of ground-based logging. Tree felling and breaking out have been identified as the most common tasks involved in serious harm injuries and fatalities.
Harvesting operations on steep land need to keep pace with work demands and new technology to reduce costs and make harvesting safer. Increased mechanisation has been seen as the solution to these problems. It is more productive than manual operations and also removes people from the hazard zones in tree felling and breaking out where most accidents happen.
Mechanisation is now becoming more widespread in forests of flat and gently sloping land. From 2013 data supplied to Future Forests Research, almost half of the ground-based operations currently use mechanised tree felling. However, progress with mechanised felling on steep land has been slower due to health and safety regulations limiting machines on slopes, and a lack of suitable equipment genuinely capable of working on steep slopes.
In 2010, Future Forests Research developed a plan to form a partnership with the Ministry for Primary Industries with the aim of ‘No worker on the slope, no hand on the chainsaw’. The programme was an alliance between research providers, forest owners and forestry engineering companies. The aim was to develop equipment which would increase the manufacturing of harvesting equipment, reduce cable logging cost, and make harvesting jobs safer. In 2010 it was calculated that when implemented the programme would reduce cable harvesting costs by 25 per cent. This would create savings of eight dollars a cubic metre of wood produced, as well as reduced logging injury rates.
The research programme results
New structure for research and development
With the introduction of the levy at the beginning of this year, a new organisational structure has been put in place for forest research and development. The Forest Grower Levy Trust Board is serviced by a secretariat of the Forest Owners’ Association. A forest grower Research and Development Committee will oversee the further development of the industry’s science and innovation plan, research priority setting, and monitoring growers’ investment and fees from members in research programmes and projects.
With these changes to research management as a result of the introduction of the commodity levy, Future Forests Research stopped forest growing research from the end of March 2014. Its focus is now on the steep land harvesting programme. The programme is now funded by 34 industry members who have committed to funding the research which is not part of the commodity levy, with a contribution of $500,000 a year and $100,000 of in- kind support. This is matched by up to $600,000 a year by the Ministry for Primary Industries until mid-2016.
The programme retains its own governance under the company structure, with a smaller board of three representing the investors for intellectual property and commercial matters. However, it is managed under contract by the Forest Owners’ Association research and development manager Russell Dale, and I will continue in my role as Future Forests Research programme manager.
Details of the new research structure are in the box on page six at the end of this article. The research is split into three programmes − mechanisation on steep terrain, increased productivity of cable extraction and development of operational efficiencies. The opportunity to apply technology which is common in other industries, such as remote control and semi- automation, are being developed.
The aim is to create remote-controlled machines which can work on steep slopes and to develop safer high speed cable extraction operations. After four years, the main results have been some commercial developments for the forest industry and include −
- ClimbMax steep slope harvester
- HarvestNav low-cost on-board navigation
- Alpine Grapple, a lightweight grapple carriage
- CutoverCam advanced hauler vision system.
- ClimbMax steep slope harvester
ClimbMax steep slope harvester
The first result in the steep terrain mechanisation programme was the ClimbMax steep slope harvester. This is a feller buncher developed by Kelly Logging Ltd and Trinder Engineers Ltd in Nelson and marketed commercially by ClimbMax Equipment Ltd.
This machine can safely and efficiently harvest trees on slopes up to 45 degrees, eliminating the need for chainsaw operators on the ground. The first machine was commissioned in Nelson and the harvester was commercialised in 2013. Since then three more machines have been sold to customers in Hawke’s Bay, British Columbia and Nelson, and a fifth machine is under construction. This has also encouraged the development of many other traction winch-assisted mechanical felling and bunching options for steep land.
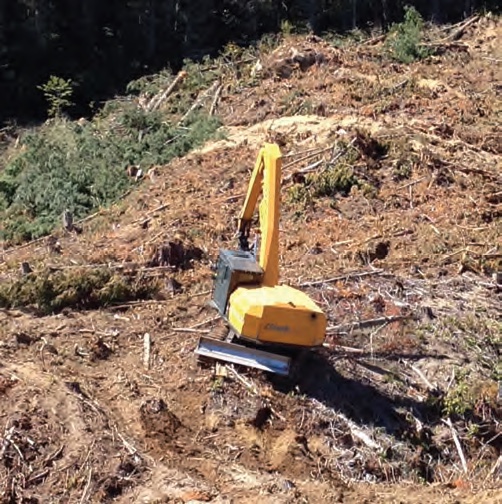
HarvestNav
Other new technology includes the HarvestNav on-board navigation for harvesting machines. HarvestNav operates on a tablet computer mounted in the cab of a harvesting machine. The GPS and digital terrain models are based on data which shows harvest area boundaries, slope and restricted areas. HarvestNav lets the machine operator track the exact location in the harvest block, and show the nature of the land ahead of the machine.
The system provides information on land around the machine including ground slope, boundaries, water courses and other exclusion zones. The app has been released to the forest industry free of charge to encourage widespread uptake and is available as a download from the Interpine Group Ltd website.
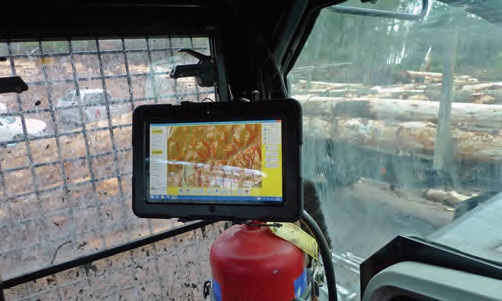
Alpine Grapple
To increase the productivity of cable extraction and eliminate manual breaking out the Alpine Grapple is aimed at improving grapple control. This hydraulic grapple carriage made by Alpine Logging of South Africa, was field tested here and modified to make it more suitable for New Zealand logging conditions. Because the grapple is non-motorised it has a lower capital cost, is lighter in weight and cheaper to run than conventional motorised grapples. It can be fitted to existing cable haulers and swing yarders. It is now available from LogPro Limited, Alpine’s New Zealand agent who has so far sold five units.
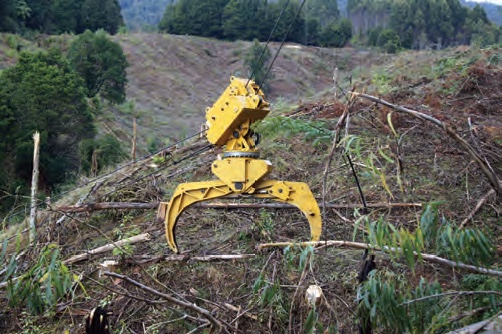
CutoverCam
The most recent product to be completed and commercialised is the CutoverCam, an advanced hauler vision system. This involves a camera linked by wi-fi to a monitor in the hauler cab showing live video of the hauler operation to the operator. With the new cameras mounted to grapple carriages which are also available commercially, the days of the hauler operator relying on just radio and tooter signals are over.
The hauler operator now has high resolution video coverage of the breaking out zone, and can control the camera remotely to pan from side-to-side, and tilt up and down or zoom in and out to see where personnel are on the cutover before beginning the inhaul cycle. For more details see the article starting on page seven.
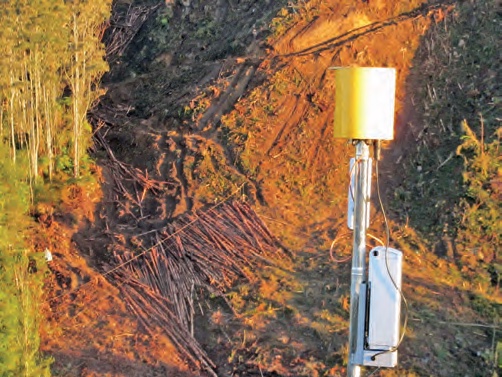
Other new products
The results of the steep land harvesting programme have involved developing technology which to some extent was already there, and to make harvesting on steep country more attractive and safer for workers. What is in the pipeline from now through to 2016 is some novel work looking at ways of harvesting wood from steep land with completely new systems. This includes remote control and tele-operation control beyond line-of-sight, felling machines, a new prototype bi-ped felling machine, and a yarding system to improve the productivity and safety of cable harvesting systems.
Recent focus has been on the installation of a tele-operation control system into a commercial feller buncher. The first stage of the project, remote-controlled tree felling, was achieved in late June 2014 and the initial field testing showed promise. This application of remote control to a tracked feller buncher on steep land is believed to be a world first.
Work with Scion and the University of Canterbury is helping develop a sensor guided bi-ped felling machine for steep country. This will have manoeuvrability and sophisticated sensing and control technology for semi-autonomous operation from safe working distances, reducing risk to harvesting workers.
A new grapple carriage designed for increased payload is also under development. A prototype, which aims to haul two tree stems every hauler cycle, should be ready for field trials early next year. A concept design for a new yarding system has recently been completed involving three new carriage designs and a remote control system. Construction of the first prototype is underway.
Programme results
These new products are giving some of the results for the original steep land harvesting programme. An example is that in initial field trials, the ClimbMax machine has shown an increase in the volume of logs cut and ready for extraction of 65 tonnes each day. This is a 26 per cent increase in productivity, and a nett cost saving of approximately $3.50 a tonne compared to conventional harvesting methods.
The capital cost of the ClimbMax harvester is high at around $1.2 million, and needs high daily production to balance the owning and operating costs. However it still has potential for small-scale harvesting operations if it can be used on two or more forestry blocks which are close together. The machine can move from one block to the next, felling enough wood to keep ahead of the cable extraction operation and maintain high production. This is an example of where small-scale foresters can collaborate on the timing of their harvest to reduce costs.
Safer and more productive
Grapple extraction has advantages over manual breaking out with chokers. These advantages include being very productive over short distances and being safer by eliminating manual breaking out. A study in 2013 showed that in manually felled or un-bunched trees the productivity of the Alpine Grapple at haul distances of up to 250 metres exceeded that of the manual breaking out system by 35 per cent. The cost of extraction was also lower by three dollars a cubic metre.
The key to improving hauler productivity is bunching trees for extraction. In this study the productivity of grapple yarding doubled compared to extracting un-bunched trees with a grapple, due to 50 per cent larger haul size in bunched wood.
Use mechanisation now
The research has demonstrated the productivity, cost and safety advantages of mechanised felling and grapple extraction. Forest owners should use these systems widely wherever land and safety considerations allow as they lead to safer operations, improved hauler productivity and reduced costs.
The best thing about the research programme is that it has helped start other developments in new forestry equipment. When Future Forests Research began in 2007, there was little innovation in harvesting. Since 2010, the programme has become a catalyst to get others to think more about all aspects of tree felling and extraction and to develop new products to improve safety and productivity for everyone’s benefit. We are starting to see greater adoption of mechanised harvesting on steep land. Now about 65 per cent of tree processing in cable operations is mechanised and almost half of ground-based operations use mechanised tree felling.
The current steep land harvesting programme is aimed at high production, low-cost and safe harvesting. But 25 per cent of production forest is small-scale forestry made up of blocks of less than 1,000 hectares. High production harvesting may not be feasible in many of the small scattered blocks, with constraints such as power lines, fences and water supplies, or poor access for large machinery. A new programme could be targeted at more cost-effective harvesting of these small forests. There is an opportunity for small forest growers to participate in the development of a small- scale harvesting research programme by taking part in a workshop scheduled to take place in Rotorua in late November. This will be after a range of safety and research reviews has been completed.
Keith Raymond is Harvesting Programme Leader at Future Forests Research Ltd based in Rotorua.
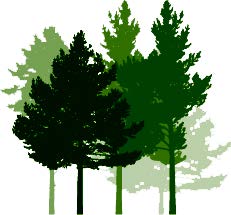